Beulaville NC Heating & Air Conditioning Services
Expert Local HVAC Services in Beulaville, NC
Jackson & Sons is the go-to team for heating and air needs in Beulaville, NC. Our team of experts is highly trained and knowledgeable in providing air conditioning and heating repairs, replacements, new installations and maintenance. Plus, we offer a range of other services such as indoor air quality products, ductwork repair and installation, and dryer vent cleaning.
If you're looking for a trustworthy HVAC company with a wide range of services, look no further than Jackson & Sons. Our company prides itself on being the top-rated HVAC company in Eastern North Carolina, and it's not hard to understand why. Our same-day service when possible and commitment to customer satisfaction make us a top choice. Not only do we offer quality services, but we also care about our community. We invite you to check out some of our reviews below from customers near you. If you're ready to get started, simply call our team now at (919) 636-6222 .
Local Reviews
for Beulaville, NC
Customers say: The reviews exhibit a positive overall sentiment, with a significant number of reviews expressing satisfaction and praise for the services provided by Jackson and Sons. The positive reviews highlight aspects such as excellent service, polite and informative technicians, quality installations, and friendly and helpful office staff. The recurring themes in the positive reviews include professionalism, punctuality, and the ability to address customer concerns effectively. However, there are also a few negative reviews, which primarily focus on issues such as delayed response times, scheduling conflicts, and dissatisfaction with the quality of work. The negative reviews mention specific instances where customers experienced problems or were not completely satisfied with the services provided. Overall, the sentiment of the reviews is positive, with a slight inclination towards the positive side. The recurring themes in the positive reviews indicate that Jackson and Sons generally provides high-quality services and strives to meet customer expectations. However, it is important to note that the negative reviews should not be overlooked, and the company should continue to work towards improving its services and addressing any issues that may arise.
Our Reviews by City
Excellent Service 🙂
Advantage - Beulaville, NC 28518
Great service! Norman was very respectful, informative, and helpful. Did a wonderful job. Thank you again!
BeulavilleNC28518 34.93-77.7725



Will keep using!
LOGAN - Beulaville, NC 28518
Technician was thorough and helpful. Very knowledgeable. Also the calling team was very helpful and kept me updated
BeulavilleNC28518 34.8575-77.755



Excellent Service, Highly recommend
Edith - Beulaville, NC 28518
Running approximately 20 minutes late. Office called and informed me that was case. Josh was very pleasant and explained service call and answered my questions. He also assisted me in turning a water filter that I was not strong enough to turn. He went above what was required and really was an example of good service.
BeulavilleNC28518 34.93-77.765



Great service Courteous repair person.
EMK - Beulaville, NC 28518
I realized issue with AC late in evening, Called next morning for service, and repairman was at house by 2pm. I was called prior to arrival so I knew when to expect the service person. Service person was courteous, answered all my questions, and had repair completed in approximately an hour. Great service.
BeulavilleNC28518 34.93-77.765



Excellent Service
Ekeyes - Beulaville, NC 28518
Arrived on time. Explained everything in detail. Wore shoe covers inside. Offered to assist me in bringing a very large box inside that had been delivered. I appreciate this courteous gesture so much. Mr Thomas was courteous throughout service call.
BeulavilleNC28518 34.93-77.765



Great job
HORNE - Beulaville, NC 28518
BeulavilleNC28518 34.8625-77.65




Awesome service
HUGHES - Beulaville, NC 28518
Great service as always.
BeulavilleNC28518 34.9375-77.8125



Excellent Service
DAVLIN - Beulaville, NC 28518
They came out quick and same day. Very friendly customer service and explained the issue well. I always have a great experience! I highly recommend this company.
BeulavilleNC28518 34.8875-77.7125



Great service!
HUGHES - Beulaville, NC 28518
BeulavilleNC28518 34.9375-77.8125




Excellent Service and Awesome technician!
Corey - Beulaville, NC 28518
Luis was very professional and very good at explaining the service he was providing. He let us know what he was doing and checking every step of the way and let us know the different options we could take when he was done. We will definitely be using Jackson & Sons again for any future HVAC service and maintenance. Luis went above and beyond and made this a great experience!
BeulavilleNC28518 34.8625-77.6375



Great tech
DEWARD - Beulaville, NC 28518
Awesome
BeulavilleNC28518 34.9375-77.8125



Deward
DEWARD - Beulaville, NC 28518
Awesome service!
BeulavilleNC28518 34.9375-77.8125



Good service. Very nice
RACHEL - Beulaville, NC 28518
Very nice
BeulavilleNC28518 34.925-77.77



Jason was awesome!
DEWARD - Beulaville, NC 28518
Awesome Tech
BeulavilleNC28518 34.9375-77.8125



Great Service.
Gene - Beulaville, NC 28518
Very polite and knowledgeable about my HVAC system.
BeulavilleNC28518 34.9275-77.765



Very professional
Randy - Beulaville, NC 28518
Tyler was very professional and courteous
BeulavilleNC28518 34.925-77.765



Kind considerate great service on time answered questions we ask
Sam - Beulaville, NC 28518
BeulavilleNC28518 34.93-77.8475




Great service
Brenda - Beulaville, NC 28518
BeulavilleNC28518 34.93-77.8475




Super great service
Kim - Beulaville, NC 28518
Caleb was very professional and explained in detail the problem and was able to fix it. We are repeat customers for a reason.... the service is great. Thank you Caleb.
BeulavilleNC28518 34.94-77.7725



Prompt and courteous service
Richard - Beulaville, NC 28518
BeulavilleNC28518 34.9175-77.785




Great service
Sam - Beulaville, NC 28518
Satisfied with service
BeulavilleNC28518 34.93-77.8475



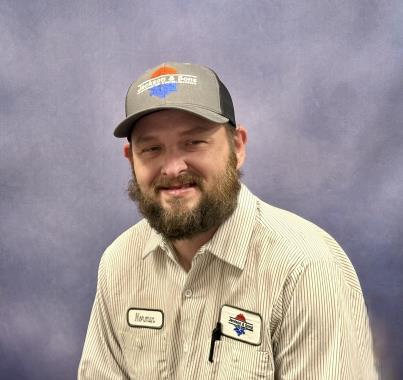
Norman A.
I replaced a shower thread p trap with a glue trap.
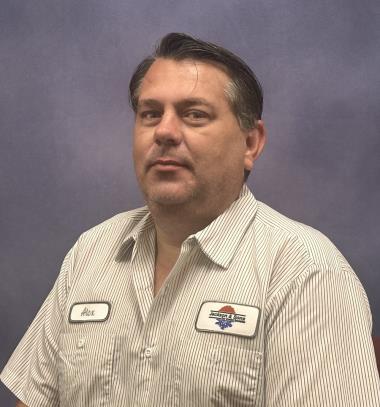
Alex R.
Found a lake under the house. The whole drainage plumbing system under the house needs to be removed and re-piped properly to resolve all the issues from water leaking under the house. Advise customer that it needs to be re-piped and she said they had a handyman that they were going to get to patch the plumbing due to them wanting to sell the house. Looked at her kitchen sink leaking and discovered that she needs a new kitchen faucet to resolve the leak for the kitchen sink.
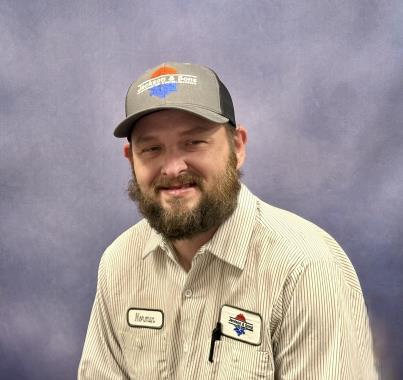
Norman A.
Found leak to be on 2 in drain line it appears someone knew it was leak there because they put tape to try to fix it did repair
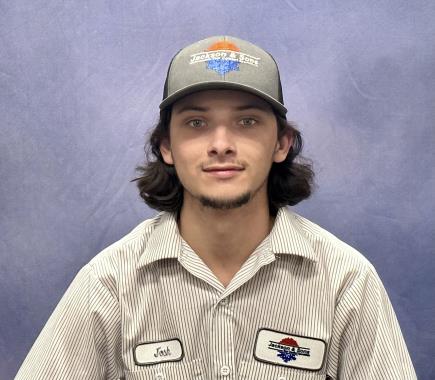
Josh W.
Tech arrived and found fuse blown in air handler, tech checked for low voltage short and found low pressure switch wire had rubbed through and shorted to metal. Tech taped and replaced fuse and system came on and began to operate properly.
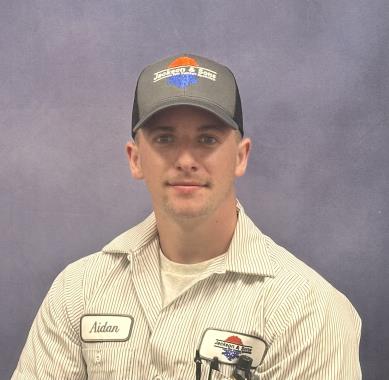
Aidan T.
- Tech was informed that the system makes a loud whirring sound at night, customer suspects it’s during defrost. - Tech cycled system through defrost 3 times and observed no abnormalities except for the fan motor making a high pitched sound when ramping up. Fan motor FLA is 0.93 amps, currently drawing 1.04 amps, indicating early failure. Confirmed warranty expires in 2026 and recommended replacing the motor. Customer opted to wait until next service visit to replace if needed. System is operating normally at this time.
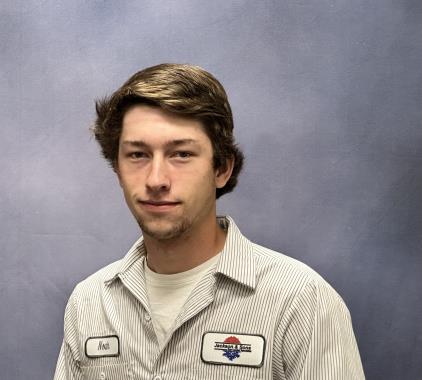
Noah C.
Upon arrival tech found split system condenser not receiving a call for heat. Found system in a lockout. Reset system and condenser attempted to start, found failed 40/5MFD dual run capacitor. Provided estimate on repair, customer will call when ready to make repair. Recommend investing in maintenance agreement.
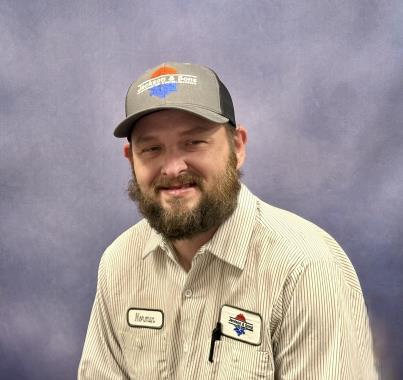
Norman A.
Ran the snake through the toilet and cleared the blockage.
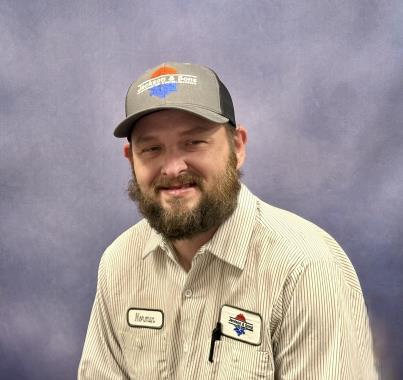
Norman A.
Replace t&p valve
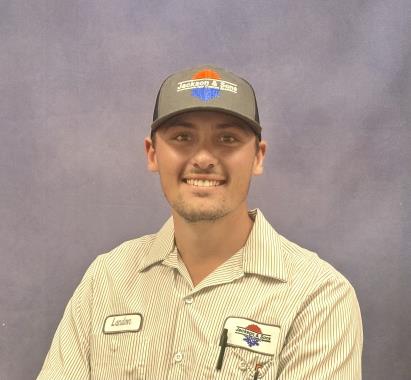
Landon C.
Tech preformed preventative maintenance and serviced system. Tech found 5mfd capacitor on condenser to be weak. Tech recommended replacing. Customer did not invest at this time. Customer invested in PSA Annual renewal. System is up and running with a delta t of 21.
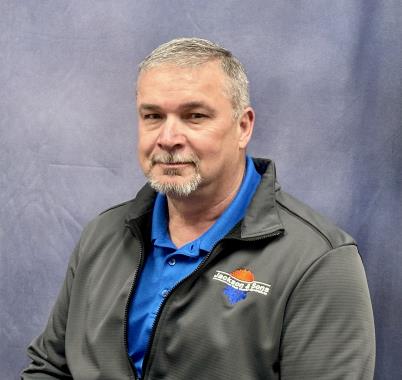
Chris M.
Came to quote a new water heater… customers has leak on old water heater pop off valve and wants it fixed and also quote a new 49 gallon water heater.
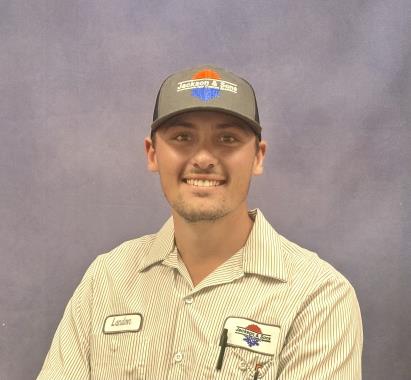
Landon C.
Tech preformed preventative maintenance and serviced system. Tech recommended plasma air to enhance indoor air quality and help eliminate viruses. Customer would like to speak with spouse before investing. System is up and running with a delta t of 21.
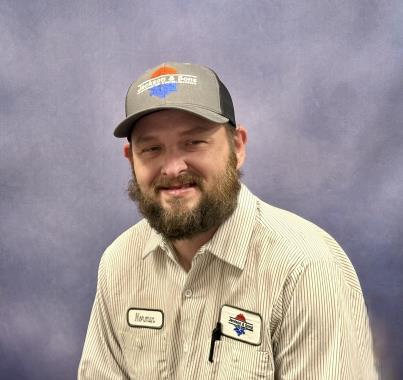
Norman A.
Leak from house of garbage disposal Customer want garbage disposal remove and sink re plumbing rest Advise all I could do for electrical part is cap wires off
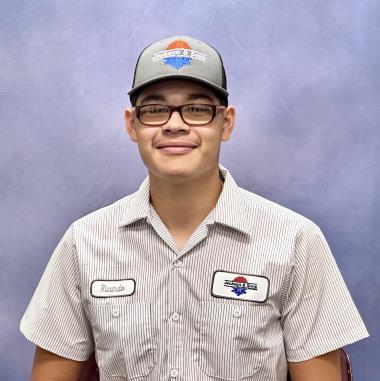
Ricardo T.
Tech washed and serviced unit and found blower dirty and housing starting to peel. Tech replaced uv bulb and re routed to return side coil. Tech found no further challenges at this time.
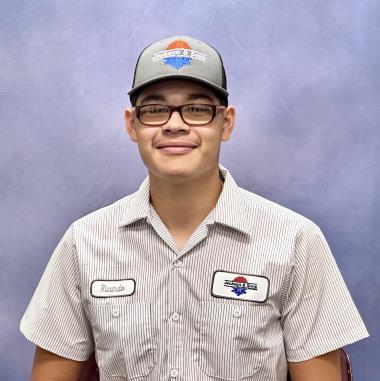
Ricardo T.
Tech washed and serviced unit and found no challenges at this time. Customer uses their own filters.
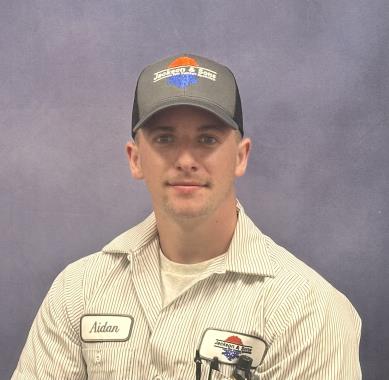
Aidan T.
- Tech found tripped 30A electric furnace breaker in sub panel upon arrival. System was replaced in March; first time operating heat. - Furnace breaker is 60A, drawing 44.8 from the 30A breaker in the sub panel, causing it to overheat and trip. - Tech received approval and upsized sub panel breaker to 60A and confirmed proper system operation with 20 minutes of run time using heat strips. - Customer invested in a monthly premium service agreement for one split system heat pump. Customer is interested in improving indoor air quality. Tech installed two 16x20x1 filters on A-frame coil. System is operating normally at this time.
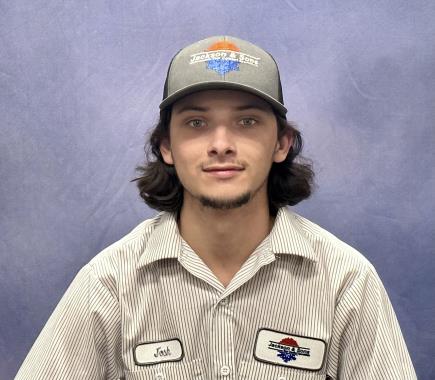
Josh W.
Tech explained thermostat operation and how zoning works for system, customer no longer wants to remove zoning or replace thermostat. Customer paid for both properties with one check.

Audonel G.
Install Trane 3 Ton Package Unit With WiFi Programmable Thermostat With Surge Protector
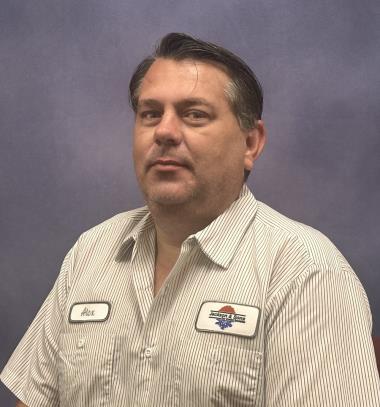
Alex R.
Turn on the drain line from the kitchen all the way to the grease tank out back of the building clogged full and stopped up not draining. Also mop sink outside of backside of building was not draining. Also fixed a leaking faucet in the kitchen. Cleared all drains mentioned above with sewer machine and everything is draining properly.
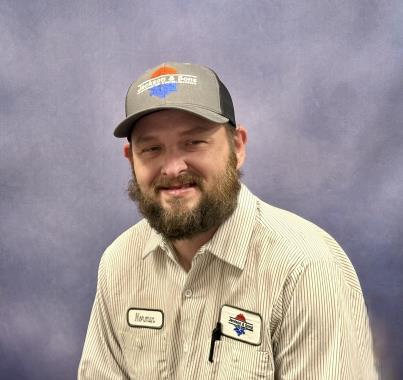
Norman A.
Brake was off for water heater turn breaker on and wait 15 min to make shore everything was okay in next 45 min should have hot water
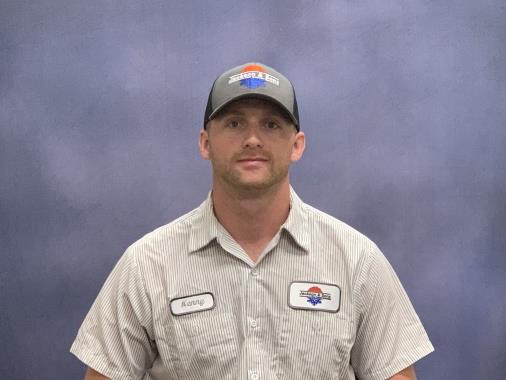
Kenny C.
Performed ESA, tech found no issues at today’s visit. Homeowner extended PSA maintenance renewal. Found uv bulb in package unit needed for replacement, homeowner declined. Systems are back on and heating.
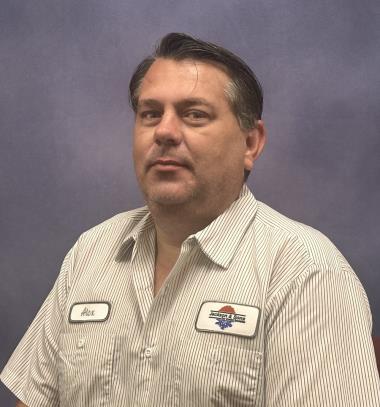
Alex R.
Found a busted Polly fitting under the house. Removed the Polly fitting and replaced it with new pex fittings and pipe.
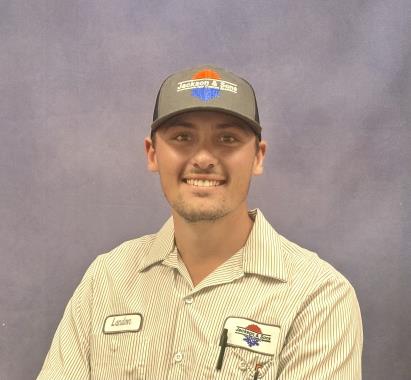
Landon C.
Tech preformed preventative maintenance and serviced system. Tech recommended ESA Plan to keep system running efficiently and properly. Customer invested in ESA Annual Plan. System is up and running with a delta t of 20.
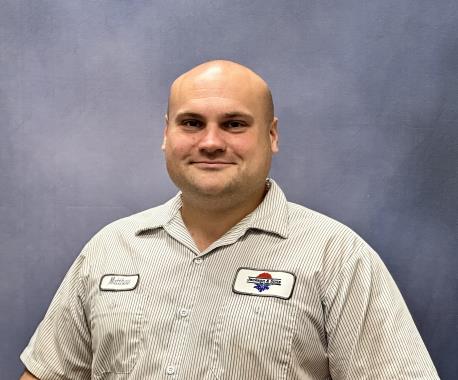
Matthew L.
Found a broken pipe hit by lawnmower in yard. Customer requested I cap the line underground so line could not get hit again.
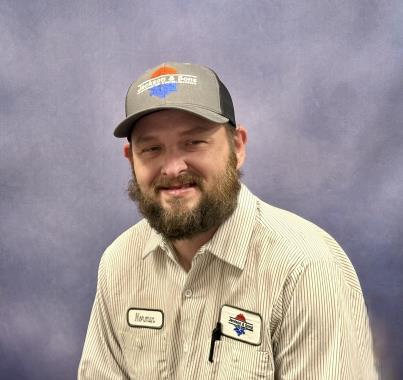
Norman A.
Ran drum snake three times to clear line Drainer fast but still gurgled to go down so crawl under house found abs drain line to be back grade replaced drain line everything working great
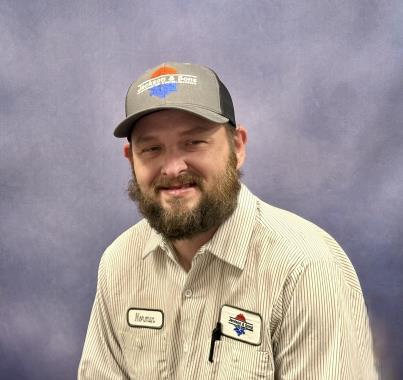
Norman A.
Pull toilet wax ring was also gone and toilet supply line was also leaking For sewer smell advise keep water in p traps even if sink aren’t be used just put some water in there ever few days For septic poor drainage is due to septic location when it rains it get cover in water not let the septic operate as it should. Was give CEO number to call to get payment no answer