Smithfield NC Heating & Air Conditioning Services
Residential HVAC Services You Can Trust in Smithfield, NC
At Jackson & Sons, we've been keeping homes comfortable since 1974 and take pride in being your trusted HVAC partner. Our commitment to excellence, family values, and community focus sets us apart in the industry. When it comes to residential HVAC services in Smithfield, we've got you covered. Contact us today to get started on heating & air conditioning service you'll love!
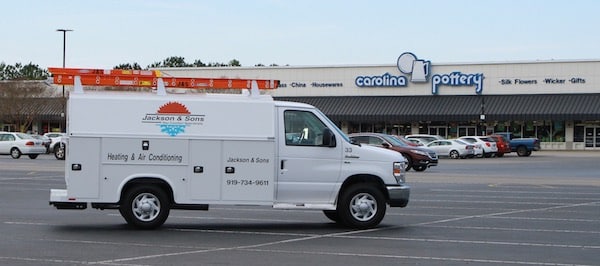
Furnace & AC Solutions in Smithfield, NC
Jackson & Sons specializes in providing top-notch residential HVAC services tailored to your needs. Whether it's a scorching summer day or a chilly winter night, our team is here to ensure your home remains a haven of comfort year-round. Our range of services includes:
Smithfield Air Conditioning Repair and Replacement
Is your air conditioner not cooling effectively? Do you need a replacement? Our skilled technicians are ready to diagnose and fix any AC issues you may have. We offer swift air conditioning repairs and efficient replacements, utilizing top-quality, energy-efficient systems to keep your home cool and energy bills low.
Full Furnace and Heat Pump Services in Smithfield, NC
When winter arrives you want a reliable heating system to keep your family warm. We offer comprehensive furnace and heat pump services, from installations to repairs and maintenance. Our experts ensure your heating system operates efficiently, delivering warmth when you need it most.
Indoor Air Quality Products & Services
We understand the importance of clean, healthy indoor air which is why we offer a range of indoor air quality solutions to enhance your home's atmosphere. From air purifiers to dehumidifiers, our products and services help you breathe easy and maintain a healthier living environment.
When You Need Us - We'll Be There!
We take pride in our prompt and reliable service. When you require HVAC assistance, Jackson & Sons is just a call away. Our commitment to customer satisfaction means:
- Same-Day Service: We understand that HVAC emergencies can happen at any time. That's why we strive to provide same-day service whenever possible. Your comfort is our top priority!
- Highest Rated HVAC Company in Eastern NC: Our dedication to excellence has earned us the reputation as the highest-rated HVAC company in Eastern North Carolina. We are honored to serve our community and uphold this standard of excellence.
- Community-Focused: Our company values the sense of community. We treat our customers like family and take pride in giving back to the community that has supported us for decades.
- Since 1974: With over four decades of experience, we have honed our skills and expertise to provide the best HVAC services possible. Trust us to deliver reliable and efficient solutions for your home.
Jackson & Sons is more than just an HVAC company; we're your neighbors and friends. We understand the unique climate challenges in Eastern NC and are dedicated to ensuring your home remains comfortable and efficient throughout the seasons. When it comes to your comfort needs, choose Jackson & Sons – your trusted partner for heating and cooling solutions in Smithfield.
Contact us today at (919) 636-6222 to schedule your HVAC service or consultation!
Local Reviews
for Smithfield, NC
Customers say: The reviews exhibit a positive overall sentiment, with a significant number of reviews expressing satisfaction and praise for the services provided by Jackson and Sons. The positive reviews highlight aspects such as excellent service, polite and informative technicians, quality installations, and friendly and helpful office staff. The recurring themes in the positive reviews include professionalism, punctuality, and the ability to address customer concerns effectively. However, there are also a few negative reviews, which primarily focus on issues such as delayed response times, scheduling conflicts, and dissatisfaction with the quality of work. The negative reviews mention specific instances where customers experienced problems or were not completely satisfied with the services provided. Overall, the sentiment of the reviews is positive, with a slight inclination towards the positive side. The recurring themes in the positive reviews indicate that Jackson and Sons generally provides high-quality services and strives to meet customer expectations. However, it is important to note that the negative reviews should not be overlooked, and the company should continue to work towards improving its services and addressing any issues that may arise.
Our Reviews by City
Excellent service by Spencer
Smithfield - Smithfield, NC 27577
SmithfieldNC27577 35.5175-78.325




Excellent
Josh - Smithfield, NC 27577
Very fast, polite and nice.
SmithfieldNC27577 35.5675-78.365



Perfectly done
Robert - Smithfield, NC 27577
Tyler knows what’s best. Go team
SmithfieldNC27577 35.4675-78.2625



Excellent service by Spencer
Smithfield - Smithfield, NC 27577
SmithfieldNC27577 35.5175-78.325




Bryce was very helpful & professional.
ROOKS - Smithfield, NC 27577
SmithfieldNC27577 35.475-78.335




Great job
Patrick - Smithfield, NC 27577
Kenny was spectacular, as always Jackson and sons delivers great service. Cannot speak highly enough about the people here.
SmithfieldNC27577 35.48-78.43



Great
Thurman - Smithfield, NC 27577
Landa n and landing grt get job
SmithfieldNC27577 35.51-78.325



Excellent service
Hali - Smithfield, NC 27577
Extremely professional and kind
SmithfieldNC27577 35.505-78.405



Great technition.
DORMAN - Smithfield, NC 27577
Told me all I needed to know.
SmithfieldNC27577 35.4875-78.3675



Prompt and Efficient Service
STATE - Smithfield, NC 27577
SmithfieldNC27577 35.5125-78.335




Excellent service
STATE - Smithfield, NC 27577
Excellent service
SmithfieldNC27577 35.5125-78.335



Excellent and professional service
CRAYTON - Smithfield, NC 27577
SmithfieldNC27577 35.525-78.3675




Amazing from start to finish
Patrick - Smithfield, NC 27577
I initially contacted Jackson and Sons for an emergency ticket for my upstairs unit. Derek came out and was outstanding, then after being told my downstairs unit would need to be replaced entirely, I had Caleb and Joshua out to my house who informed me the unit could be serviced, and didn’t need to be replaced at all. I cannot speak highly enough about the service I received from everyone within the company, so much so that I signed a one year maintenance plan on the spot. Jackson and sons, and specifically the three people mentioned above, have earned a customer for life. Great customer service, and honest people who show true integrity at every turn! I’ll tell anyone and everyone who ever asks to call Jackson and Sons for any hvac needs from here forward.
SmithfieldNC27577 35.48-78.43



The Best Service Ever
BOOTH - Smithfield, NC 27577
Jackson & Sons always does a great job. Josh, my technician today, was nice and explained everything he was going to do as well as everything he did. I am very pleased with my experience with Josh. Many thanks to Jackson & Sons and their wonderful employees for always giving their best!
SmithfieldNC27577 35.495-78.36



Excellent service
CHINNIS - Smithfield, NC 27577
SmithfieldNC27577 35.4075-78.2275




Excellent Service!
Cydney - Smithfield, NC 27577
SmithfieldNC27577 35.53-78.4325




Service was great .
London - Smithfield, NC 27577
Josh was knowledgeable and explained everything that needed to be done. Very pleasant person. I would like to have Josh next service time.
SmithfieldNC27577 35.4875-78.3675



Great service!
3HC - Smithfield, NC 27577
SmithfieldNC27577 35.515-78.325




Great service!
3HC - Smithfield, NC 27577
SmithfieldNC27577 35.515-78.325




Always Great Service
OPW - Smithfield, NC 27577
SmithfieldNC27577 35.555-78.3825




Great Job
OPW - Smithfield, NC 27577
Jesse always does a great job servicing our units.
SmithfieldNC27577 35.555-78.3825
Response from Jackson & Sons:
Thanks for sharing your review with us and the community.




Excellent service
Robert - Smithfield, NC 27577
SmithfieldNC27577 35.5225-78.3175




Always Great Service
OPW - Smithfield, NC 27577
Michael did a great job finding our issue.
SmithfieldNC27577 35.555-78.3825



Excellent Service As Always
SIMMONS - Smithfield, NC 27577
Kenny did a great job. This is our second time with him as our service man. He’s courteous and very professional.
SmithfieldNC27577 35.53-78.3425
Response from Jackson & Sons:
It was a pleasure serving you and your family. We really appreciate you taking the time to share your feedback with us and the community.




Homeowner
Ann - Smithfield, NC 27577
Great service
SmithfieldNC27577 35.5-78.355



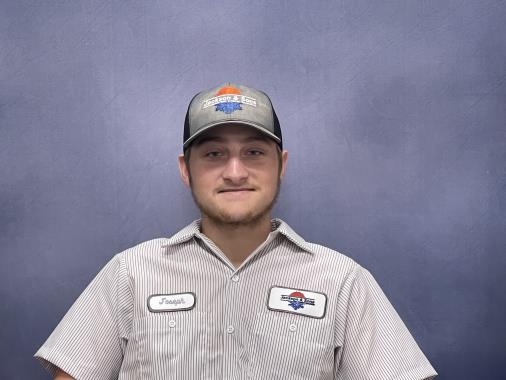
Joseph C.
Tech performed CMA on 9 air handlers at today’s visit, will need to return to finish, tech found system 13 frozen over and after de iced tech found failed indoor TXV no metering refrigerant properly. Customer wants TXV ordered and replaced as soon as possible.
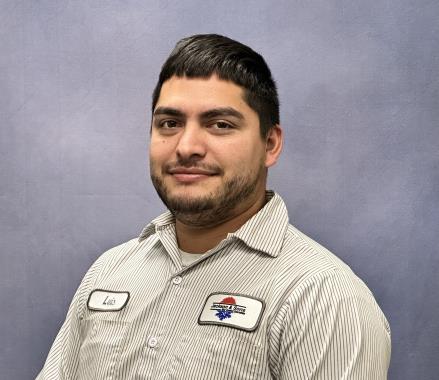
Luis R.
Technician found unit 2 and unit 3 new systems were giving alarm fault code. Technician found the control for the smoke detectors had wiring reversed technician corrected and fault codes cleared. Technician replaced orfices and adjusted gas regulator to get inlet pressure to 12wc and outlet pressure was 10.52wc. Technician cycled system and heat kicked on no issues.
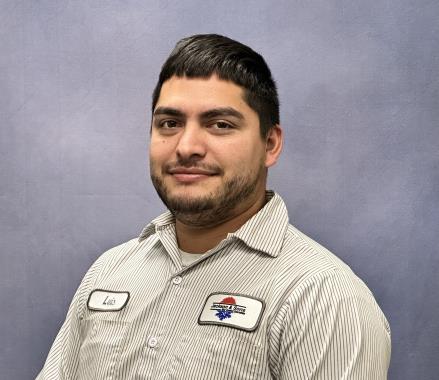
Luis R.
Technician replaced 3 pole contactor. Found install had pressurized system and added 410a to break the vacuum. Technician was informed install added 7lbs will need to return with 2 drums of 410a and refrigerant oil to add to each circuit.
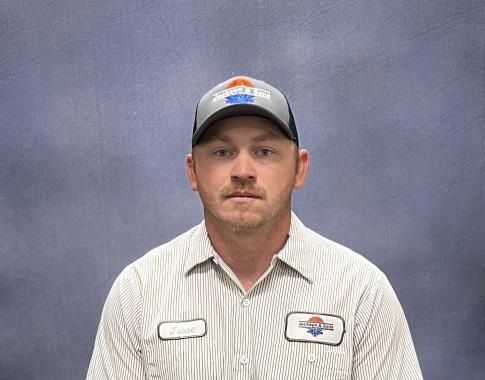
Jesse J.
Replace (2) Trane 25 Ton Package A/C Units With (2) New Trane 25 Ton Package A/C Units With (2) WiFi Programmable Thermostats
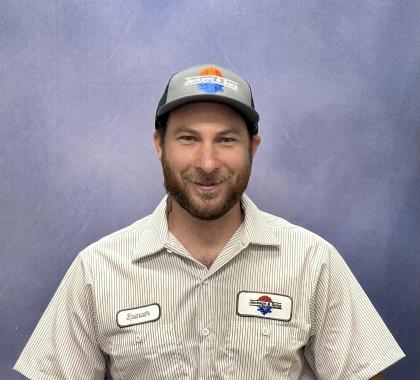
Spencer C.
Tech performed CMA full service and replaced filters. Tech found the following issues and gave repair quotes; Blown uv bulb AHU 1 training building Furnace 10 UV bulb is blown, waiting on gas orifices. Furnace 9 zone board temp sensor is reading much lower, can cause issues with locking out on low supply when ac is running. AHU 17 drain pan is cracked ,preexisting issue. Pitted contactor 3a condenser. Out of tolerance capacitor on condenser 2a replaced under contractor warranty Out of tolerance fan capacitor on condenser 16, 4.3/5 Failed condenser fan motor mini split condenser 21. Customer approved replacing zone sensor. This sensor is on the furnace beside the one that needs the orifice repair.
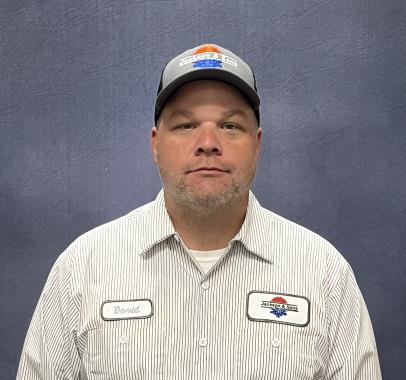
David S.
— Return to perform repairs as approved on estimates from prior maintenance: — Replace Outdoor Fan Motor & Capacitor on CU-2. — Swap supply registers at ceiling locations in Beauty Salon and Laundry Room. Found that supply duct sizing does not match. Office should provide estimate to install new 10” register damper at Beauty Salon location. Customer requested to close off Beauty Salon register with cardboard until part arrives.

Kyle W.
Unit #6F unable to access inside of apartment, found reversing valve wiring removed from solenoid. Re-secured wire and system switched over to cooling. O tstat wire for reversing valve looks to have been jumped with R in the past, likely due to issues with thermostat or wiring. System is now cooling, but may not heat unless manually switched at reversing valve. Darryl is aware of situation.
Mike A.
Tracy unavailable until this evening left proposal with mother
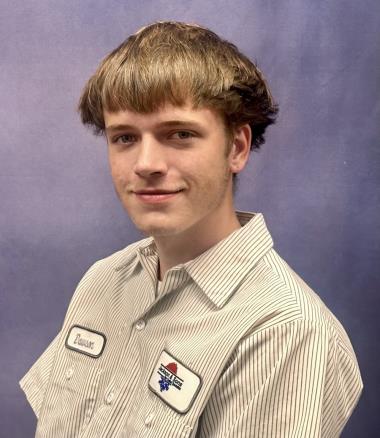
Dawson M.
Tech serviced and cleaned unit. Tech found evaporator coil to be severely rusted. Tech did a detailed leak search and found a consistent leak. Tech called field supervisor out to get another set of eyes. Tech found compressor side of capacitor getting close to threshold 48.2/45. Tech faced no other challenges this visit. Unit is struggling to get up to temperature. Tech could only get a delta t of 16 for heat.
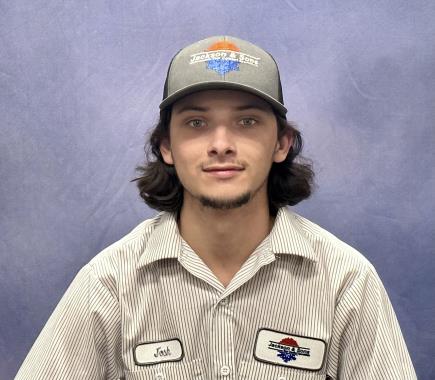
Josh W.
Tech performed esa on one system, tech did not find any challenges with system at todays visit. System is back on and operating properly at this time.
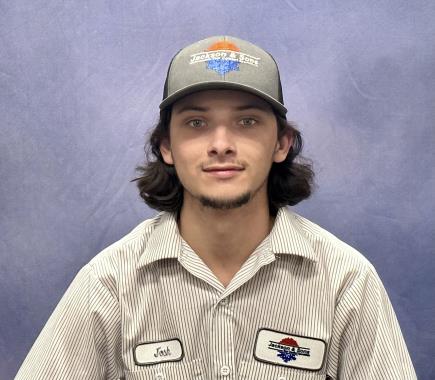
Josh W.
Tech arrived and had to wait for second company to get here, tech showed second company what wires were taken loose. Tech spoke with office and stated second company was taking care of smoke detector codes.
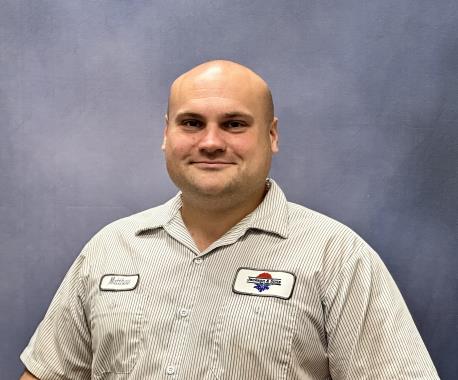
Matthew L.
Tech replaced exhaust fan motor in ventilation unit above room 415. Tested without issue. Tech billed for repair. Replace Exhaust Fan Motor
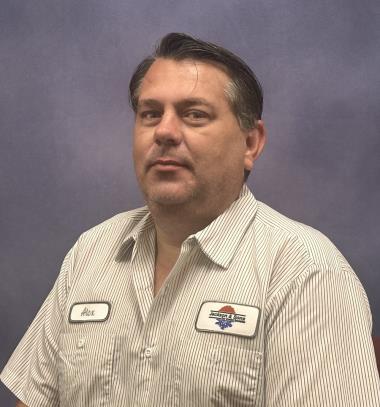
Alex R.
Pulled up the toilet and got can out then reset toilet.
Jerry H.
3/7…..Waited on inspector no show 3/10….inspector came out. Checked electrical and all three are good. Unit 2 passed smoke test and electrical. Unit 1 did not shut off with smoke test. Detector Needs checked and pre smoked! Unit 3 blower is not running. Need fuses for air handler on unit 3 to get it running and pre smoke unit 3 and unit 1.
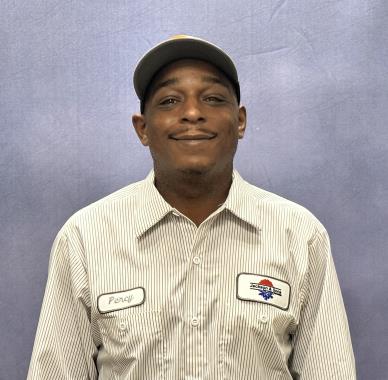
Percy M.
Performed CMA Inspection on 1 gas furnace a/c split system. - System is performing and heating properly at this time and has a delta T of over 20degrees. - Tech completed filter change of 6-20x20x1 fikters and flushed drain lines. - There were no challenges found on todays visit. - There are pictures and a performance report attached to this invoice.
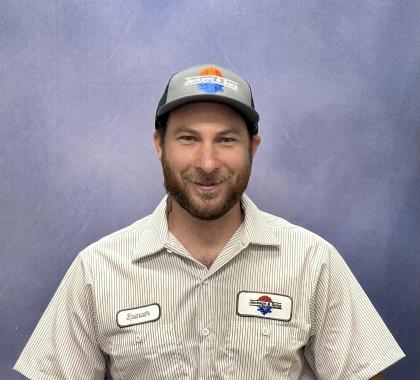
Spencer C.
Tech found contactor pulled in but condenser not running. Tech found disconnect left out. Customer stated they had a maintenance by another company. Tech put disconnect in and found normal operation, tech suspects system has only been running emergency heat since then.. Tech recommended maintenance plan. Customer agreed to monthly esa.
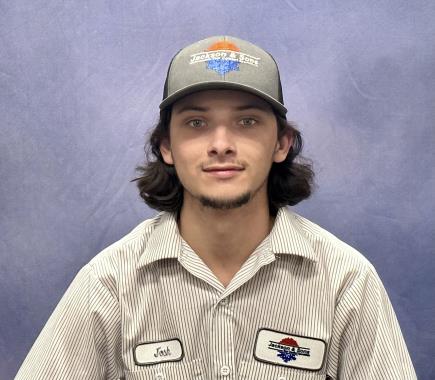
Josh W.
Tech performed esa on inside portion of systems, tech did not find any challenges with operation, tech replaced filters and informed customer of rescheduling for outdoor section.
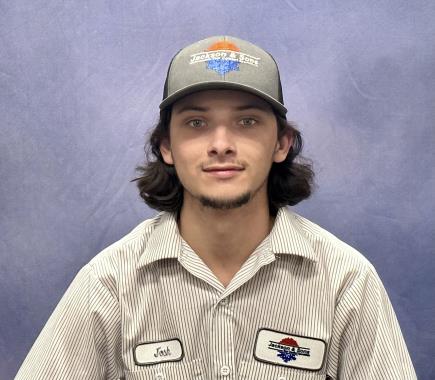
Josh W.
Tech arrived and performed esa on one system. Tech found no issues at today’s visit. System is back on and operating properly at this time.

Chris A.
Tech washed and serviced unit. Found no challenges at this time. Left customers extra filters. Unit is h9ld8gn a delta T of 20
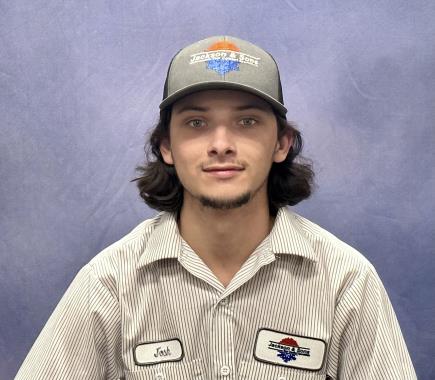
Josh W.
Tech found damper 5 was wired ins series between damper and unit, tech checked wiring and tested that damper opens and closes. Tech found no issues with damper wiring.
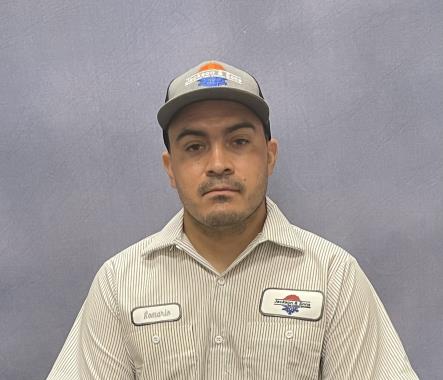
Romario T.
Tech performed diagnostic on furnace 3, tech found system calls for heat but inducer does not kick on, tech also found gas line to pilot has crack and will need to be flared. Tech spoke with office about someone coming out to flare and repair gas line and finish diagnostic of system.
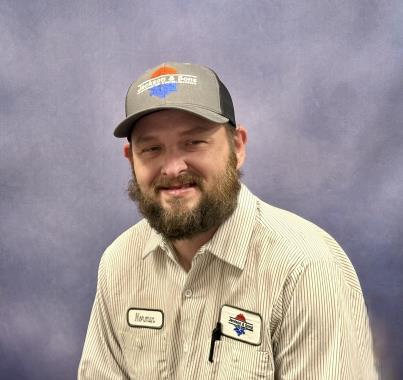
Norman A.
Found leak come from tite shower liner advise we don’t remove old tite showers and replace
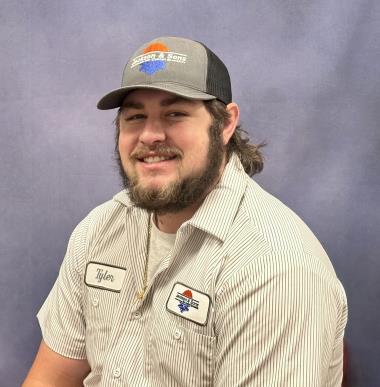
Tyler T.
Tech washed and serviced units per service agreement, upon arrival tech found duel run capacitor to be testing weak on compressor side of the upstairs condenser, tech recommended replacement customer declined, tech left estimates, both systems are back up and running and holding a delta t of 20+ degrees upon departure, customer has washable filters
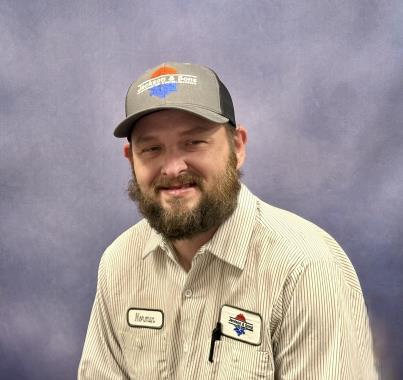
Norman A.
Got one urinal work and shut off the other we will have to get a whole urinal flush valve kit with sud washer
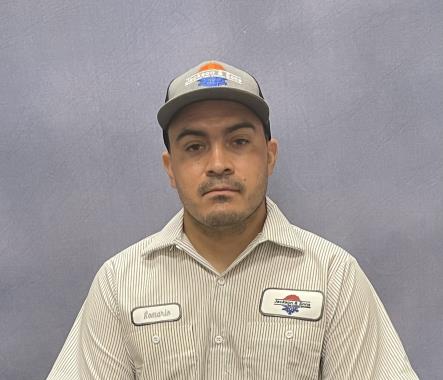
Romario T.
Tech replaced 27 gas regulators, tested for gas leaks and passed. Serial#111423S71G model#TUD1B060A9361AB gas furnace needs a LP conversation kit, customer stated that we installed the system, current office size is 45 and needs a 56 on all 3 burners and the LP spring. All tube heaters, gas furnaces and paint booth system are back heating. Customer supplied all regulators. Adam will prove final pricing.