Fremont NC Heating & Air Conditioning Services
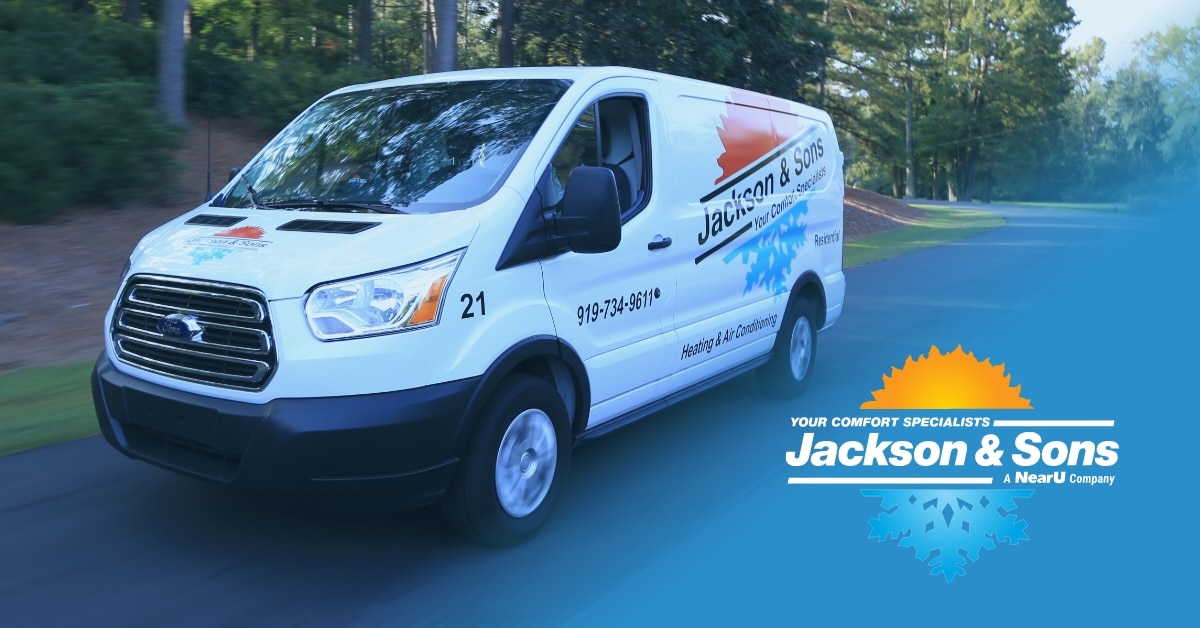
Expert Local HVAC Repair and Installation Service in Fremont, NC
Are you tired of sweating through the summer months or shivering in your own home during the winter? Look no further than Jackson & Sons for all of your Fremont home HVAC needs. Our highly trained technicians specialize in air conditioning repair and replacement, ensuring that your home stays cool and comfortable even on the hottest days.
And when winter rolls around, we've got you covered with heating repairs, installations and maintenance. But our services don't stop there - we also offer indoor air quality products, ductwork repair and installation and even dryer vent cleaning.
With our reliable service and competitive pricing, choosing Jackson & Sons is an easy choice. And, in serving Eastern North Carolina since 1974, we're dedicated to giving back to our community and ensuring that our customers are always satisfied. Don't believe us? Check out our reviews below from happy customers near you. Let us help you stay comfortable in your own home, no matter the season.
Call today at (919) 636-6222 for HVAC repair, replacement, maintenance and indoor air quality service in Fremont or contact us online with any questions!
Expert Plumbers in Fremont
Plumbing problems are never fun. Whether it’s a clogged drain, a leaky pipe, or a water heater that suddenly stops working, you need a plumber you can trust. That’s where Jackson & Sons comes in.
Our experienced, licensed plumbers show up ready to fix the problem and get your home’s plumbing back on track—quickly and professionally.
Need a plumber in Fremont? Call us now at (919) 636-6222 or contact us online with questions about your plumbing service!
Plumbing for Kinston Homeowners
We offer a wide range of plumbing services, including:
-
Drain cleaning and hydro jetting
-
Sewer line inspection and repair
-
Water line replacement
-
Fixture installation (sinks, faucets, toilets)
-
Garbage disposal repair
-
Water heater installation (tank and tankless)
-
Plumbing for remodels and new construction
Get the Best Plumbing, Heating and AC Repair Service in Fremont
When something goes wrong with your plumbing or HVAC system, you want a team that shows up fast and knows what they’re doing. That’s where we come in. We’re your go-to crew in Pikeville, NC for dependable plumbing, heating, and AC services—whether it’s a small fix or a big job.
We believe in doing the job right the first time. No guesswork, no runaround—just real help when you need it.
Local Reviews
for Fremont, NC
Customers say: The reviews exhibit a positive overall sentiment, with a significant number of reviews expressing satisfaction and praise for the services provided by Jackson and Sons. The positive reviews highlight aspects such as excellent service, polite and informative technicians, quality installations, and friendly and helpful office staff. The recurring themes in the positive reviews include professionalism, punctuality, and the ability to address customer concerns effectively. However, there are also a few negative reviews, which primarily focus on issues such as delayed response times, scheduling conflicts, and dissatisfaction with the quality of work. The negative reviews mention specific instances where customers experienced problems or were not completely satisfied with the services provided. Overall, the sentiment of the reviews is positive, with a slight inclination towards the positive side. The recurring themes in the positive reviews indicate that Jackson and Sons generally provides high-quality services and strives to meet customer expectations. However, it is important to note that the negative reviews should not be overlooked, and the company should continue to work towards improving its services and addressing any issues that may arise.
Our Reviews by City
Excellent service, prompt and courteous
LC - Fremont, NC 27830
Ricardo did a great job.
FremontNC27830 35.575-78.0475



Great Service
Anne - Fremont, NC 27830
Professional, Knowledgeable, was able to answer all my questions
FremontNC27830 35.54-77.9675



Great Service
BRYANT - Fremont, NC 27830
Knowledgeable, Professional, Courteous
FremontNC27830 35.54-77.9675
Response from Jackson & Sons:
Thanks for sharing your review with us and the community.




Great Service
Ricky - Fremont, NC 27830
FremontNC27830 35.5675-78.05
Response from Jackson & Sons:
We’re delighted to hear about your recent experience with us and we’re so pleased that you recommend our services. Thank you for taking the time to share your experience and we look forward to welcoming you back soon!




EXCELLENT JOB
Donnie Walston - Fremont, NC 27830
FremontNC27830 35.5425-77.9725




EXCELLENT JOB
Donnie Walston - Fremont, NC 27830
FremontNC27830 35.5425-77.9725




GREAT SERVICE
Wanda - Fremont, NC 27830
FremontNC27830 35.5425-77.9725




Great
Jimmie - Fremont, NC 27830
FremontNC27830 35.535-77.875




Excellent service….very dependable!
Marie - Fremont, NC 27830
Kyle Williams is a great service technician. Thorough performing his work and shows great concern for customer’s needs and safety. Kyle is a PROFESSIONAL HVAC TECHNICIAN!
FremontNC27830 35.5325-78.045



A very good service experience
Eddie - Fremont, NC 27830
Arrived in a timely manner, did quality work in a timely manner.
FremontNC27830 35.5425-77.9725



Maintenance
Amy - Fremont, NC 27830
Thanks
FremontNC27830 35.535-77.875



Excellent service, always going the extra mile.
LUCAS - Fremont, NC 27830
Chris was outstanding with taking care of Mom's request. he went above and beyond the scope of the visit.
FremontNC27830 35.575-78.0475



Excellent service
COE - Fremont, NC 27830
Ricardo was very friendly and made me feel comfortable with his service. I would love to have him come again.
FremontNC27830 35.53-78.0675



Great service
Ariel - Fremont, NC 27830
Logan was great. He is friendly, knowledgeable, & a hard worker!
FremontNC27830 35.525-77.985
Response from Jackson & Sons:
Thank you so much for taking the time to leave us a 5-star review!




Excellent service
LUCAS - Fremont, NC 27830
FremontNC27830 35.575-78.0475




Great service
LUCAS - Fremont, NC 27830
FremontNC27830 35.575-78.0475




Excellent service
PRICE - Fremont, NC 27830
Very polite and explained everything to me
FremontNC27830 35.5175-77.855



Excellent, prompt service
LUCAS - Fremont, NC 27830
FremontNC27830 35.575-78.0475




Great service
LUCAS - Fremont, NC 27830
FremontNC27830 35.575-78.0475




Excellent work
LUCAS - Fremont, NC 27830
Quick response, very courteous tech, quickly diagnosed the problem.
FremontNC27830 35.575-78.0475



Excellent service
PRICE - Fremont, NC 27830
Always have great experience and would never go anywhere else
FremontNC27830 35.5175-77.855



Best service
PRICE - Fremont, NC 27830
Jackson and son is the best and will not do business anywhere else. Caleb is the best
FremontNC27830 35.5175-77.855



Excellent service
PRICE - Fremont, NC 27830
FremontNC27830 35.5175-77.855




Great service
Corey - Fremont, NC 27830
FremontNC27830 35.5825-77.915




EXCELLENT SERVICE!
ALEXANDER - Fremont, NC 27830
My tech was very knowledgeable and very professional. Zero complaints, I'll keep using Jackson & Sons for all of my HVAC needs.
FremontNC27830 35.515-78.02



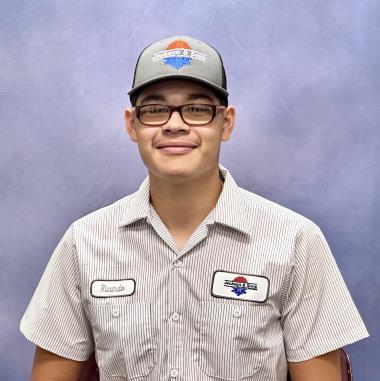
Ricardo T.
Tech washed and serviced unit and found no challenges at this time. System is back up and operating at this time. Customer will call for renewal.
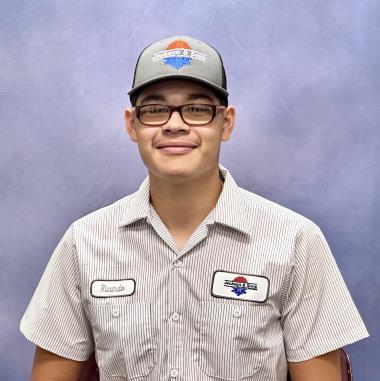
Ricardo T.
Tech washed and serviced unit and found no challenges at this time.
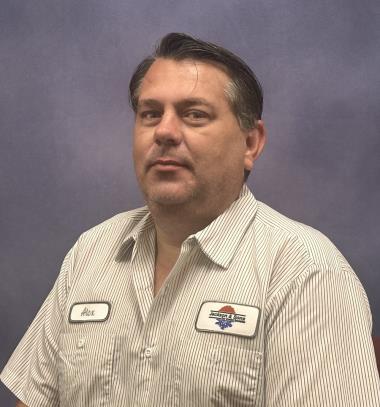
Alex R.
Found three handle shower valve with busted off handles. Gave customer an estimate for replacement of the shower valve and also for installing a new handheld shower sprayer.
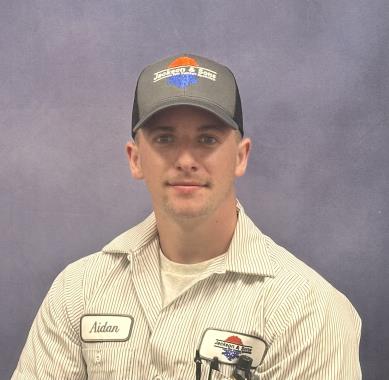
Aidan T.
— Customer reported that the LP tank was refilled around 2 weeks prior to this visit. — First ignition revealed low gas pressure in first stage at 2.20” WC. Tech adjusted to 6.54” WC, purged the gas line, decreased regulator pressure, and cleaned burners. Second stage LP pressure read 10.18 without adjustment. — Upon further inspection, tech observed the IGN board constantly sending 15V to the first stage terminals on the gas valve, with no call for heat. IGN board is faulty and needs to be replaced. — Draft inducer motor is over heating during operation but not over-amping. Tech recommends replacing the inducer motor to avoid future challenges. System is operating normally at this time with adjusted gas pressures. Service warranty.
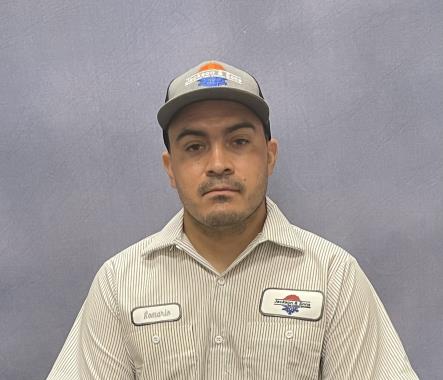
Romario T.
Thermostat was off, gas tank is only at 10% Heat exchanger has some soot build up, tested gas and heat pump. Both side are operating but tech does recommend to have the gas tank filled soon. Heat exchanger is recommended to be cleaned, system is under 2 yer warranty. Once the customer has gas filled, gas pressures may need to be checked and heat exchanger cleaned due to some build up being present.
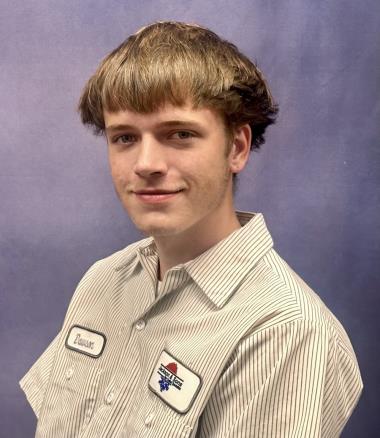
Dawson M.
Tech serviced and cleaned unit. Upon arrival tech found flame inside burner (shown in video). Tech found compressor side of capacitor reading at 43.1/40 (44=bad). Tech also found bacterial growth inside blower housing. Tech pulled and cleaned. Tech found uv bulb burnt out. Tech faced no other challenges this visit. Unit is heating and cooling efficiently. Tech recommends plasma air and replacing uv bulb. Customer would like to wait till next visit.
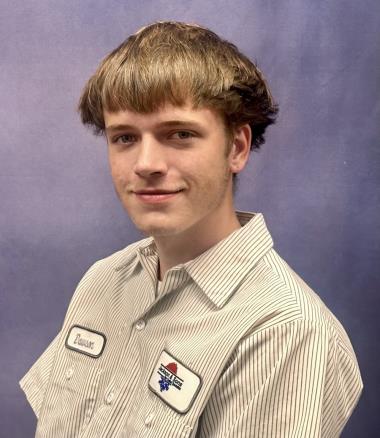
Dawson M.
Tech serviced and cleaned unit. Tech found evaporator coil to be severely rusted. Tech did a detailed leak search but could not find any leaks. Tech faced no other challenges this visit. Unit is heating and cooling efficiently. Tech informed customer about ESA renewal. Customer renewed ESA plan.

Bryce C.
Provided quote for new package heat pump. DF
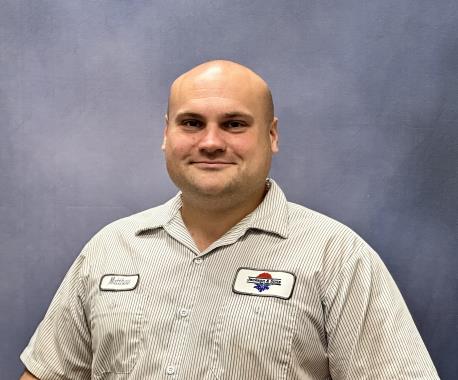
Matthew L.
Tech arrived and found low voltage fuse blown inside electric furnace after someone tried to replace thermostat due to thermostat scheduling issue. Tech tested blower and heat strips without issue. Found breaker for outdoor unit tripped. Confirmed compressor is shorted to ground. Has continuity in the megohm scale. Reset breaker and compressor did start. Tech suspects high wear and tear on compressor motor windings. Compressor is on its way out. 5uf side of 35/5uf capacitor is reading 6% weak at 4.66uf. 7.5uf blower capacitor is reading very weak at 4.6uf. We replaced a schraeder core and added refrigerant in 2022. Tested heat mode and defrost without further issues.
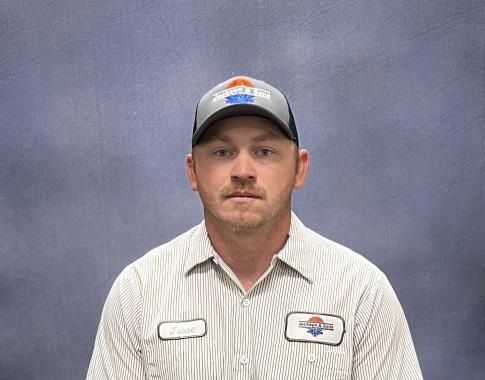
Jesse J.
Install 3.5 Ton Trane AC With Coil With 100,000 BTU Furnace With Plasma Air With WiFi Programmable Thermostat
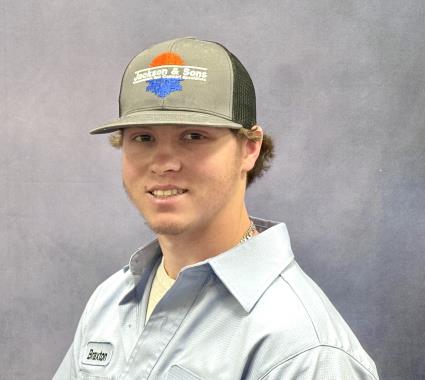
C. Braxton B.
Tech cleaned and serviced unit it tech found no challenges at this time unit is up and running customer wanted tech to leave extra filters
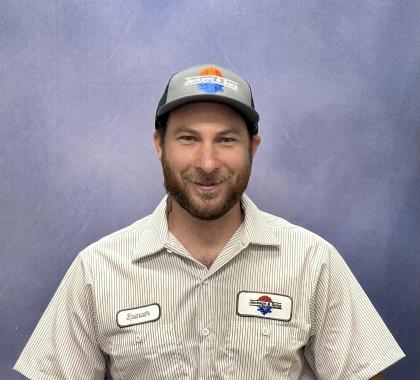
Spencer C.
Customer was confused about the hold on the thermostat. Customer does not want system programmed. Tech set thermostat to nonprogrammable and assured thermostat will not go back on hold. Tech also left thermostat manual.
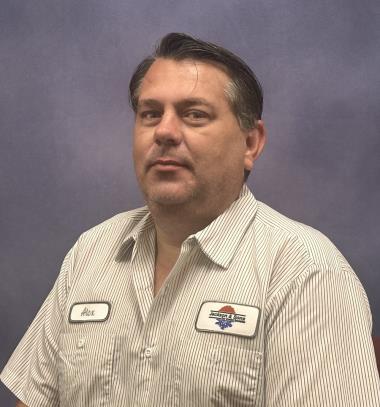
Alex R.
Look under the house to see how the drain line was ran due to the washing machine and kitchen sink backing up. Found that the washing machine drain line that also catches the sink drain is too small and needs to be upgraded up to a 3 inch pipe to be able to drain properly per current code.
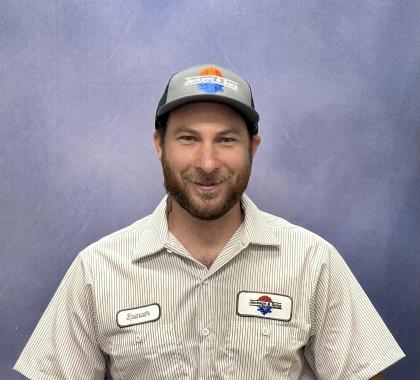
Spencer C.
Tech replaced rollout switch and found no issues heating.
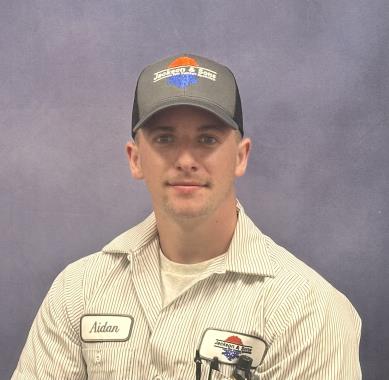
Aidan T.
{AirTemp Gas Furnace - right building front} — Tech found failed thermostat constantly energizing Y terminal and operating cool mode regardless of thermostat setting. — Recommended Focus Pro t-stat; customer will purchase their own thermostat and install it. — Tech bypassed Y circuit and confirmed proper heat operation with W circuit. System is heating normally at this time. Emailed bill.
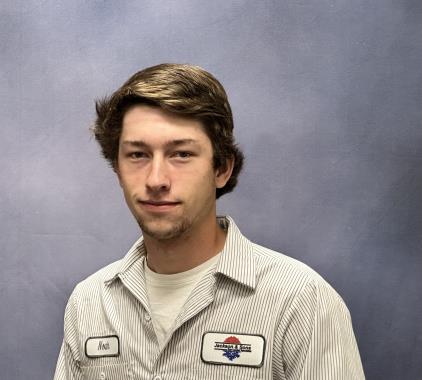
Noah C.
Upon arrival tech found indoor fan running long after system satisfied. Tech was unable to check install settings due to incorrect code on back plate. Display has been mixed up with another thermostat, tech replaced Vision Pro 8000 because of this issue and programmed system. Blower is shutting off as usual. Worry free warranty.
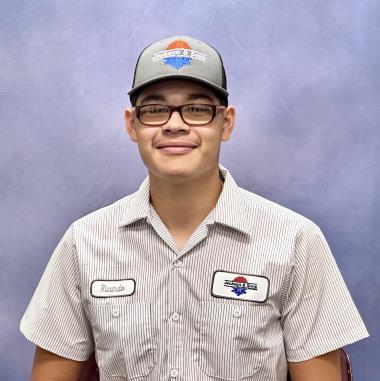
Ricardo T.
Tech washed and serviced unit and found no challenges at this time.
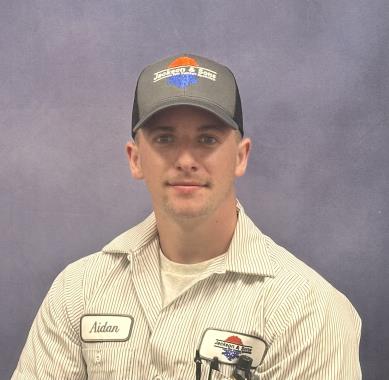
Aidan T.
{Trane Heat Pump} — Tech confirmed defrost operation upon arrival, confirmed defrost control board communicates 24V to heat strips in defrost mode, and accurate refrigerant charge. — Noted failed 104C fuse link (replaced 2 days prior) and replaced for testing. Confirmed heat strip relay operation to ensure the heat strips are not constantly energized and overheating. Observed no signs of relay failure. Visually inspected heat strips and found no issues. — Blower wheel has a small amount of microbial growth which may contribute to airflow challenges. Tech recommends pulling the blower wheel to clean it and install a coil access door to clean the indoor coil. Need to provide estimate for coil access door installation. — Noted blower capacitor reading 6.14/7.5 and built estimate. — Comfort plus service agreement expires on today’s date - only one service has been completed and customer is due for a second service. Office will schedule service for next week to perform recommended maint
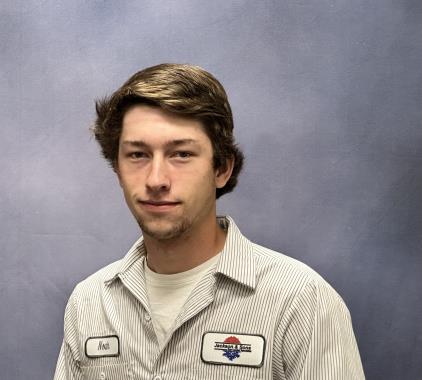
Noah C.
Tech found fault code at defrost board for ambient sensor/in timed defrost mode. Ohmed coil and ambient sensor, both tested within spec. Forced defrost without issue, found heat strip breaker in the off position causing system not to keep up and more frequently defrost causing error code. System is back up and heating, tested all system operation. Service warranty.
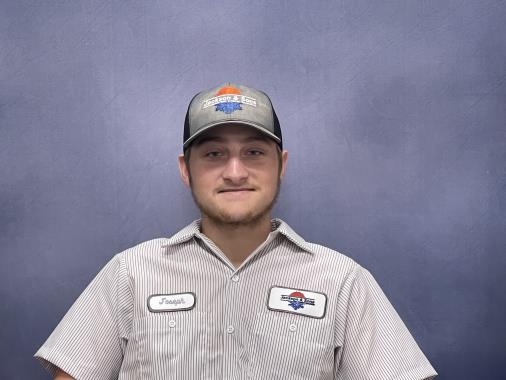
Joseph C.
Customer stated heat pump not working, tech found fuse link for heat strip broken, tech replaced and found thermostat was programmed for gas not allowing condenser to run and only run heat strips. While on site customer stated dual fuel system had also stopped working, tech inspected and found inducer motor Mount broken and gas turned off, tech fixed mount and turned gas on and cycled system with no challenges. No charge per recent visits and repairs.
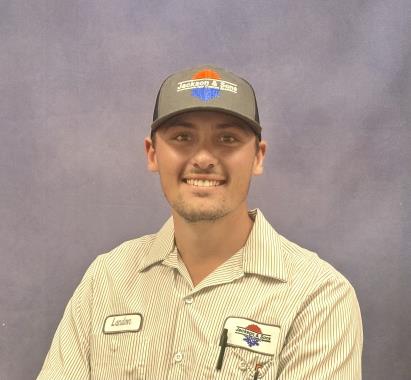
Landon C.
Provided proposal for customer for both system replacements.
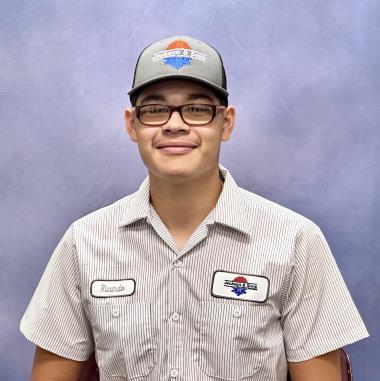
Ricardo T.
Tech washed and serviced unit and found no challenges at this time.
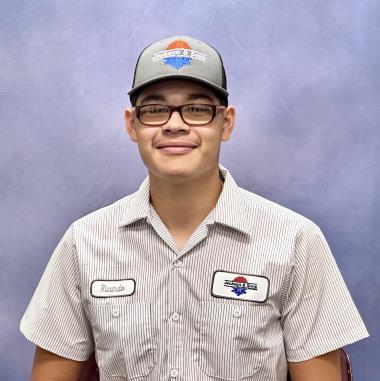
Ricardo T.
Tech serviced both inside units and found no challenges at this time. Customer provides there own filters. Customer would like to have an estimate sent to climatize crawl space. Both systems heating with a 20+ DeltaT.
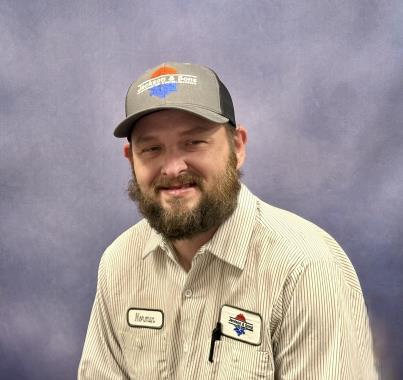
Norman A.
Ran snakke to clear kitchen drain advise about pipe under sink is not done right and that grease is not good to go in pipe
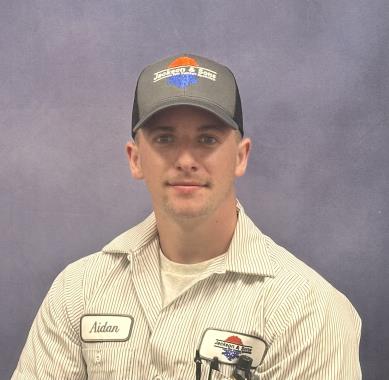
Aidan T.
Upon arrival, tech found fault code 34 for failure to prove flame. Examined gas pressures and noted only 3.42” WC at gas valve inlet and dropping down to 1.21” WC when pressure stabilized. Inspected propane tank and found 0 PSI on pressure gauge. Customer stated that the tank was filled to 50% in December. - Tech suspects there’s a leak in the gas line and advised customer to contact a gas company to perform a leak search. Tech shut gas off at the propane tank and at the shutoff valve for the furnace. - Attempted search for leaks between regulator and gas valve but could not search properly due to low pressure. Adjusted temperature cutout limit on heat pump from 40 degrees to 20 degrees until the system is repaired - Tech observed gas valve opening when 24V call is received but not providing enough pressure to ignite, resulting in non-combusted gas entering the air stream through missing/broken seals on the door panels, creating a gas scent in the left half of the home. - Recommende