Faison NC Heating & Air Conditioning Services
Expert Local HVAC Services in Faison, NC
Are you in search of a reliable heating and air company in Faison, NC? Jackson & Sons has got you covered! Our team of experts offers top-notch air conditioning and heating repairs, replacements, new installations, and maintenance. We understand how important it is to have your HVAC system working efficiently, which is why we take pride in offering same-day service whenever possible. Our team is highly trained and knowledgeable and we offer ductwork repair and installation, indoor air quality products, and dryer vent cleaning services.
What sets us apart from the competition is our dedication to our community. As a local HVAC company, we care about our neighbors and strive to provide excellent service to everyone we work with. Don't take our word for it - check out the glowing reviews below from satisfied customers near you. With Jackson & Sons, you can trust that you're in good hands. Call us today at (919) 636-6222 !
Local Reviews
for Faison, NC
Customers say: The reviews exhibit a positive overall sentiment, with a significant number of reviews expressing satisfaction and praise for the services provided by Jackson and Sons. The positive reviews highlight aspects such as excellent service, polite and informative technicians, quality installations, and friendly and helpful office staff. The recurring themes in the positive reviews include professionalism, punctuality, and the ability to address customer concerns effectively. However, there are also a few negative reviews, which primarily focus on issues such as delayed response times, scheduling conflicts, and dissatisfaction with the quality of work. The negative reviews mention specific instances where customers experienced problems or were not completely satisfied with the services provided. Overall, the sentiment of the reviews is positive, with a slight inclination towards the positive side. The recurring themes in the positive reviews indicate that Jackson and Sons generally provides high-quality services and strives to meet customer expectations. However, it is important to note that the negative reviews should not be overlooked, and the company should continue to work towards improving its services and addressing any issues that may arise.
Our Reviews by City
Excellent
Lib - Faison, NC 28341
FaisonNC28341 35.115-78.2225




Excellent Service
Claudia - Faison, NC 28341
Alex was kind an professional. I am totally satisfied!
FaisonNC28341 35.115-78.1375



Excellent
Nelson Hibbs - Faison, NC 28341
Great service guy very knowledgeable
FaisonNC28341 35.1075-78.2075



Great service!
Ashley - Faison, NC 28341
FaisonNC28341 35.2075-78.2025




Excellent
SAMPSON - Faison, NC 28341
FaisonNC28341 35.1025-78.1525




AWESOME
OAKES PAM - Faison, NC 28341
Matt was very professional and done an excellent job at servicing our heating and cooling system
FaisonNC28341 35.12-78.1425



Excellent service I truly thank ya'll 👊❤❤❤
Ruth - Faison, NC 28341
Today was my first time calling on Jackson & Son heating/Ac system & I got satisfied by Mr.Donnie he was very respectful & kind he talk with me with quality manners & got heat back going I'm very pleased!!!
FaisonNC28341 35.0975-78.16



Repair/replace
Sharon - Faison, NC 28341
FaisonNC28341 35.205-78.2125




winter check up
LOUIS - Faison, NC 28341
Wayne did a good job in diagnosing my problem
FaisonNC28341 35.1075-78.1675



Professional Service
SARAH - Faison, NC 28341
Easy and uneventful
FaisonNC28341 35.12-78.14



good job
LOUIS - Faison, NC 28341
FaisonNC28341 35.1075-78.1675




Very professional technician
Olivia - Faison, NC 28341
Glad this person was sent to service my unit. Discussed w me, component that needed replacement & handled this today, as well as doing the maintenance. My unit is 16 yrs old, tech’s knowledge of the equipment & manner of communication w the customer was reassuring. This person is an asset to the company.
FaisonNC28341 35.12-78.1425



Awesome service and Price
Barbara - Faison, NC 28341
I have a contract with Jackson and Son for over 12 years, and I am always pleased, they have a quick response time, and the service tech are always very professional. Once the tech looks over the problem called in, you will receive a price quote immediately. I would without a doubt recommend this company. KUDOS
FaisonNC28341 35.19-78.22



Tech performed the jod very well.
JOHN - Faison, NC 28341
FaisonNC28341 35.2025-78.265




winter check up
LOUIS - Faison, NC 28341
FaisonNC28341 35.1075-78.1675




Great
KING - Faison, NC 28341
FaisonNC28341 35.185-78.2125




Did good job of inspecting product
ALEXANDER - Faison, NC 28341
Appreciated the service!
FaisonNC28341 35.1175-78.1175



Great Service
Angela - Faison, NC
FaisonNC 35.1175-78.135




HVAC Service
LOUIS - Faison, NC 28341
Tech was very and informing and polite
FaisonNC28341 35.1075-78.1675



Great service
Alexander - Faison, NC 28341
The serviceman tyler was knowledgeable of job heater work well after completion .
FaisonNC28341 35.1175-78.12



Good service.
JOHN - Faison, NC 28341
Not knowing exactly what should be done and what was actually done and how well it was done makes it difficult to rate. The service man was extremely courteous and seemed very knowledgeable. But I‘ve had some bad experiences with this company so trusting that the job was completed correctly takes a considerable leap of faith.
FaisonNC28341 35.19-78.22



Great Service
ANNETTE - Faison, NC 28341
FaisonNC28341 35.2025-78.2375




Very thorough service
David - Faison, NC 28341
Very pleased with technician
FaisonNC28341 35.19-78.22



great service
ROY - Faison, NC 28341
FaisonNC28341 35.1525-78.1025




great service from tech
LOUIS - Faison, NC 28341
FaisonNC28341 35.1075-78.1675




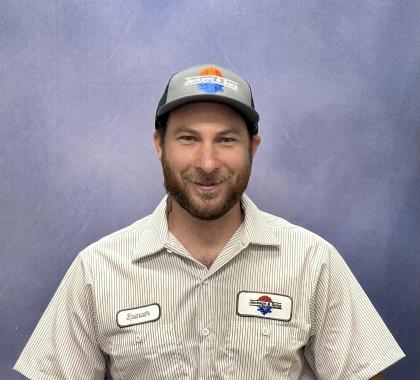
Spencer C.
Tech found a blown low voltage fuse and a short on the pressure switch wire. Tech replaced fuse, repaired short and tested system. System is heating properly, with heat pump heat only, no heat strips have ever been installed. Tech repaired short, system is now heating properly.
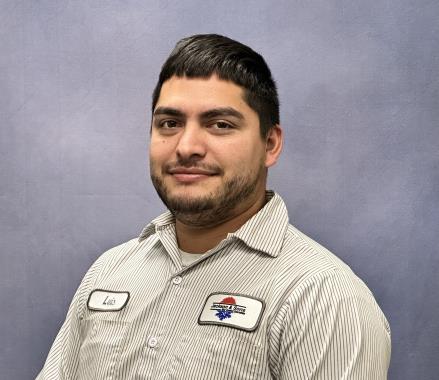
Luis R.
Tech found kitchen system was slightly frozen over. Technician found blower was not blowing. Until tech tightened the belt. Blower started to move more air. Tech spoke with maintenance guy he informed tech he replaced condenser fan motor. But motor had a lot of vibration. System is cooling maintenance guy is going to install new blades.
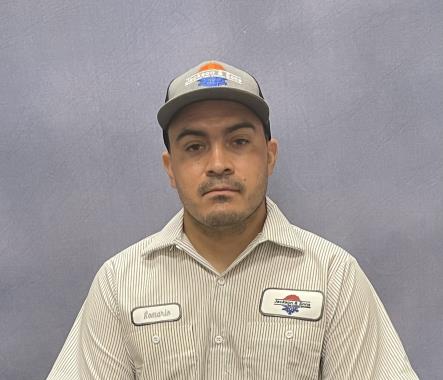
Romario T.
3 head mini split system. Main living room head indicates a C5 error code which means that is miss communication between the indoor and outdoor unit. The other 2 heads are operating properly, tech switched the wires to the outdoor unit and indoor unit to eliminate the outdoor unit being a challenge and the error code still persisted. Tech inspected the indoor control board and found corrosion on the board elements. Tech was not able to find service facts for blue ridge mini splits. Tech recommended to replace the indoor control board along with the main display transmitter. Tech informed the customer over the phone and requested quotes on replacement of the indoor control board and display transmitter and also a quote on how much would cost to replace a customer supplied mini split head if he were to get one and have us recover the system, install the mini split head and charge the system back up. Data tag for the outdoor unit was not readable and tech does not know how much refrigera
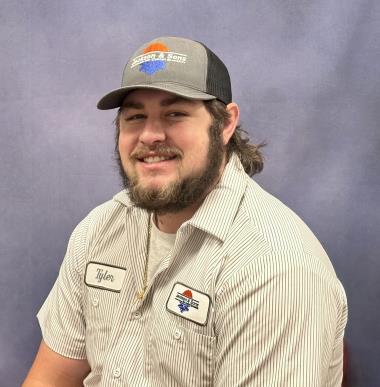
Tyler T.
Tech washed and serviced unit per service agreement, tech found no challenges with the system at today’s visit, tech found duel run capacitor starting to test low on fan side tech notified homeowner and will monitor it, the system is back up and running and holding a delta t of 20+ degrees
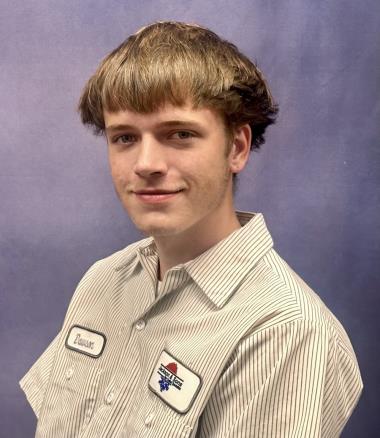
Dawson M.
Tech serviced and cleaned unit. Tech found bacteria build up on Goodman air handler. Tech pulled and cleaned. Tech found blower capacitor reading at 7.40/10. Tech recommends replacement. Tech also found evaporator coil to be severely rusted and tech found a consistent leak. Tech found Goodman condenser capacitor fan side reading at 4.27/5. Tech turned over to field supervisor. Both units are heating and cooling efficiently.

Bryce C.
Provided repair and replacement quote for split heat pump
Jerry H.
Tech cleaned and serviced unit tech could no get inside to get temps tech also could not get in crawlspace was blocked and could not inter because homeowner not home did leave filters at the door
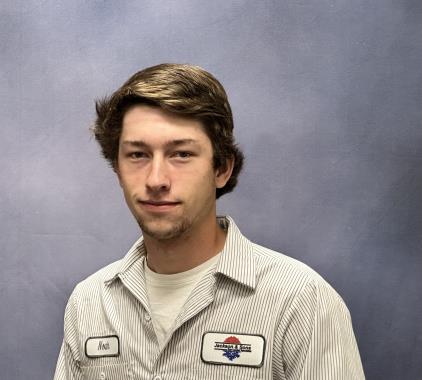
Noah C.
Found 60 amp time delay fuse blown at air handler disconnect. Replaced fuse and ran system, found no issues to cause blown fuse. System is back up and heating.
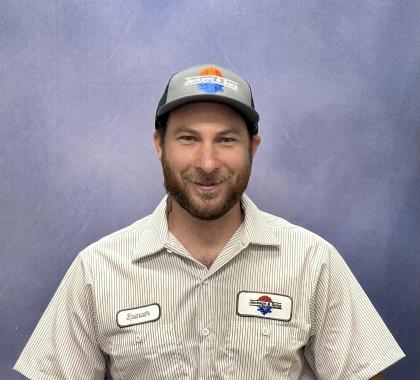
Spencer C.
Tech found thermostat is blank and 28 volts present between r and c on thermostat terminals. Thermostat has failed. Customer approved a focus pro and tech replaced. System is now heating properly.
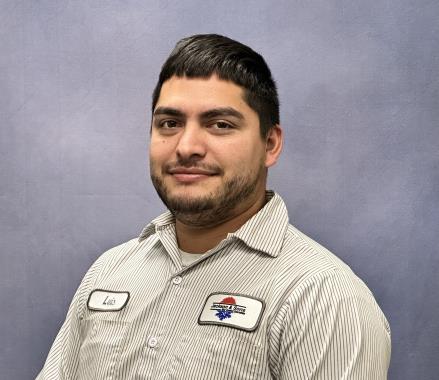
Luis R.
Tech verified pressures on system and temperatures are 68 return and 111 supply. Technician found offset was higher then normal. Technician found thermostat was satisfied at 74 but temp inside the house was 68. Tech adjusted the offset and system will be heating properly at this time.
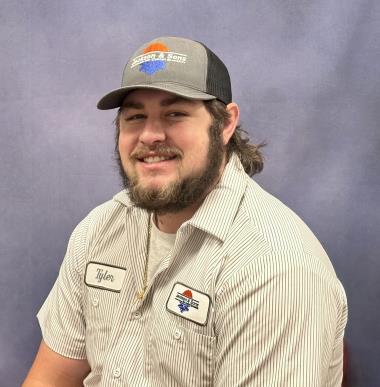
Tyler T.
Tech serviced and washed unit per service agreement, throughout inspection tech leaked searched condensing coils, tech could not pick up any solid leaks at today’s visit, tech found drain pan still leaking, customer stated was going to wait until unit needs to be replaced, the system is back up and running and holding a delta t 20
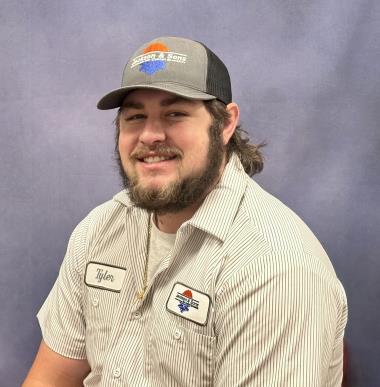
Tyler T.
Tech washed and serviced unit per service agreement, tech found no challenges at today’s visit, the system is back up and running and holding a delta t of 20+ degrees, tech spoke with customers son about replacing 50 amp breaker customer says will talk with mom and call back
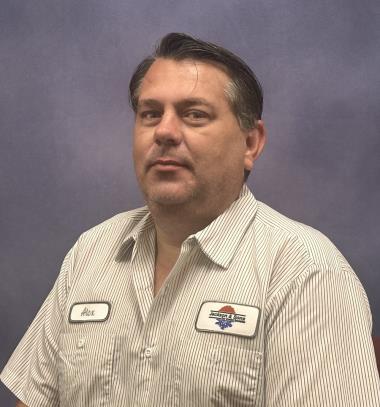
Alex R.
Found leak under the trailer to be a broken polybutylene line under the middle of the trailer. Cut out broken fittings and reconnected with new fittings and pipe.
Jerry H.
Installed 2 co monitors upstairs
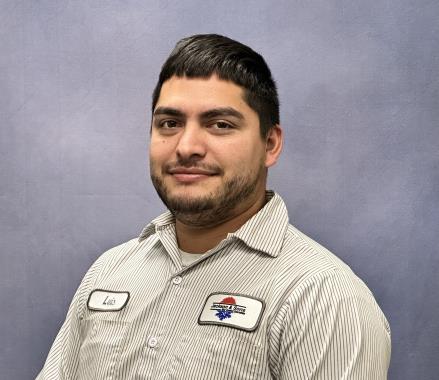
Luis R.
Technician found breaker for 1 heating element 40 amp was tripped technician reset breaker and tested system did find 1 leg pulling 30 amps and other element pulling 20 amp. Technician informed homeowner that elements are operating at this time but could be potential issues in future. System is heating at this time.
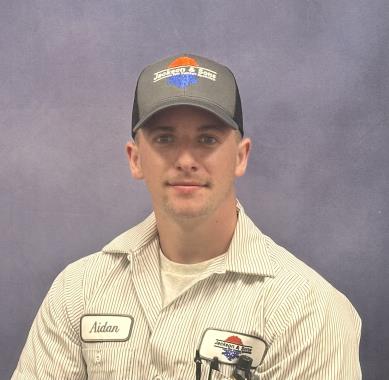
Aidan T.
- Tech found failed Vision Pro thermostat for system in maintenance office. Replaced with focus pro thermostat and confirmed proper heat strip and defrost operation. System is operating normally at this time.
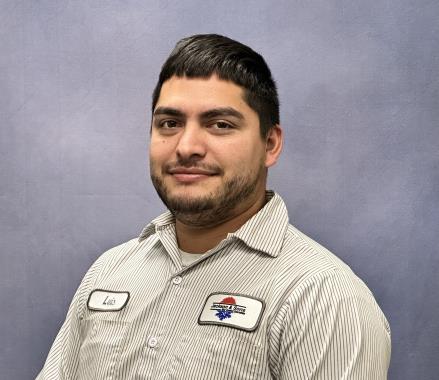
Luis R.
Technician adjusted pressure to 10.5 and 6.5 system is heating properly at 107 degrees.

Amber W.
Trane Packaged Unit (XL15) 4YCZ5048E1090A Trane, XL15 Packaged Gas/Electric, 4 Ton, Packaged Unit Quantity: 1 Other HVAC Add-Ons CUSTOM-F37KVN CO DETECTOR Quantity: 1 Other HVAC Add-Ons CUSTOM-MF3IRD Filter Dryer Quantity: 1 Other HVAC Add-Ons CUSTOM-5ZZ1CN Gas Regulator Quantity: 1 18" Start Collar Quantity: 1 50x20x27 Hood (Trane) 4T & 5T Package Unit Quantity: 1 50x60 Pad Quantity: 1 Level Pad Quantity: 1

Bryce C.
Provided repair vs replace option for customer. Customer invested in new Trane gas pack.
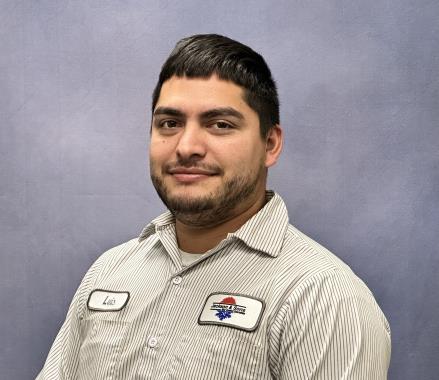
Luis R.
Technician found a leak on the coil. Technician programmed thermostat on emergency heat so customer can run gas heat to keep warm field supervisor will keep get in touch to give customer best solution
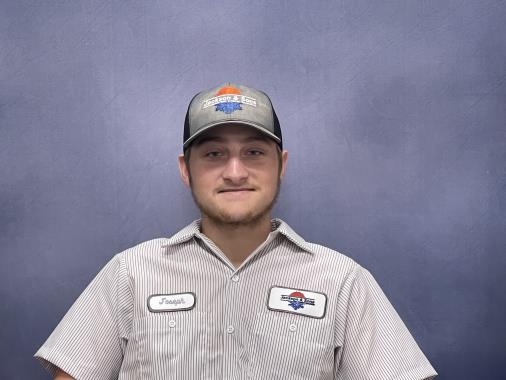
Joseph C.
Tech found dual fuel system not receiving voltage from thermostat, tech bypassed thermostat and found system operating properly. Tech replaced after approval system now back heating properly at this time. Bill per office
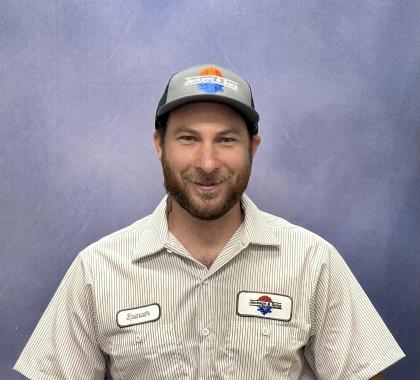
Spencer C.
Tech found manual reset roll out switch tripped. Heat exchangers are completely smutted out and need to be cleaned or replaced. Tech cleaned heat exchangers per customer request. Gas pressure is good at 10in/wc. Flame now looks and sounds good. System is heating properly. 91 supply temp with a 50 return.
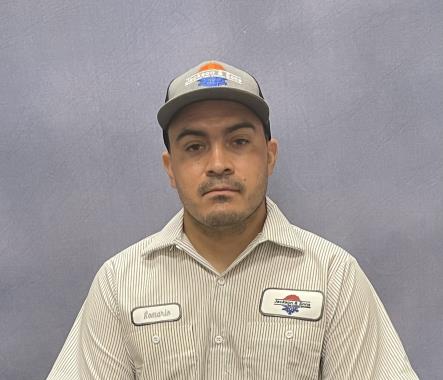
Romario T.
Replace a failed service disconnect. After repairs, tech noticed a gas odor coming from the 2008 gas package unit. Tech inspected the heat exchanger and noticed some hot spots on the tubes but no cracks or holes. Gas pressures were checked and noticed high inlet pressure of 19inWC, tech attempted to decrease the gas pressure at the regulator but did not move. Gas regulator would have to be checked and replaced by the gas company. Tech used soda bubbles around the fittings of the system but did not find any gas leak. System does have soot and recommended cleaning the heat exchanger. Estimate will be provided and sent over, gas pressures at the gas valve may need to be rechecked after the regulator gets replaced, gas pressure was decreased at the gas valve some to have the system operating for the time being.

Amber W.
Trane Packaged Unit (XL15) 4YCZ5036F1070A Trane, XL15 Packaged Gas/Electric, 3 Ton, Packaged Unit Quantity: 1 Other Services CUSTOM-0M1HWW ESA Quantity: 1 Other Thermostats CUSTOM-9HQCG8 Honeywell - Wi-Fi VisionPRO® 8000 ( Trane Split Systems) Quantity: 1 Other HVAC Add-Ons CUSTOM-F37KVN CO DETECTOR Quantity: 1 Other HVAC Add-Ons CUSTOM-5ZZ1CN Gas Regulator Quantity: 1 52x52 Pad Quantity: 1 Level Pad Quantity: 1 New Hood Quantity: 1
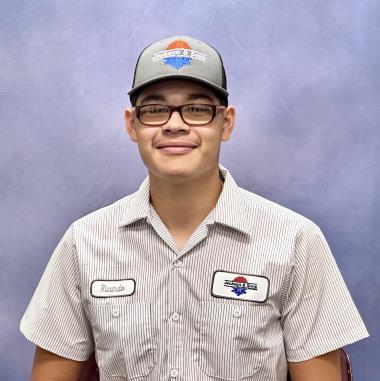
Ricardo T.
Tech washed and serviced unit and found no challenges at this time.