Rocky Mount NC Heating & Air Conditioning Services
Expert Local HVAC Services in Rocky Mount, NC
At Jackson & Sons, we take pride in offering top-quality HVAC services to our community in Rocky Mount, NC. As experts in air conditioning and heating repairs, replacements, new installations and maintenance, we believe that choosing our local HVAC company is an easy choice. Our highly trained HVAC technicians have the knowledge and experience to tackle any repair or installation with ease. We also offer indoor air quality products, ductwork repair and installation and dryer vent cleaning to keep your home running efficiently.
With same-day service whenever possible, we strive to provide convenient and efficient services to all of our customers. Our business has been proudly serving the community since 1974, which is why we are the top-rated HVAC company in Eastern North Carolina. We care deeply about our community and are committed to providing friendly, informative services to help keep your home comfortable year-round. So if you need AC repair, furnace repair or any other HVAC services, don't hesitate to call us today at (919) 636-6222 . Read some of our reviews below from other satisfied customers near you to learn more about why we're the best choice for your HVAC needs!
Local Reviews
for Rocky Mount, NC
Customers say: The reviews exhibit a positive overall sentiment, with a significant number of reviews expressing satisfaction and praise for the services provided by Jackson and Sons. The positive reviews highlight aspects such as excellent service, polite and informative technicians, quality installations, and friendly and helpful office staff. The recurring themes in the positive reviews include professionalism, punctuality, and the ability to address customer concerns effectively. However, there are also a few negative reviews, which primarily focus on issues such as delayed response times, scheduling conflicts, and dissatisfaction with the quality of work. The negative reviews mention specific instances where customers experienced problems or were not completely satisfied with the services provided. Overall, the sentiment of the reviews is positive, with a slight inclination towards the positive side. The recurring themes in the positive reviews indicate that Jackson and Sons generally provides high-quality services and strives to meet customer expectations. However, it is important to note that the negative reviews should not be overlooked, and the company should continue to work towards improving its services and addressing any issues that may arise.
Our Reviews by City
Best in 10 years
Local restaurant owner - Rocky Mount, NC 27804
Aiden went above and beyond to help find a solution to a recurring problem. My best experience with a tech yet.
Rocky MountNC27804 35.9625-77.8325



Excellent Service
Michael - Rocky Mount, NC 27803
Rocky MountNC27803 35.945-77.855




Hmmmmm🤔🤔🤔🤔
Bernice - Rocky Mount, NC 27801
Price & problem questionable
Rocky MountNC27801 35.955-77.755



Questionable 🤔🤔
Bernice - Rocky Mount, NC 27801
I felt like I was pulled through a ringer !!! Professionals take advantage of seniors and single women. We need heat asap. Yesterday was questionable also.
Rocky MountNC27801 35.955-77.755



Excellent service
Heritage - Rocky Mount, NC 27801
He took the time to explain every detail to us very good service
Rocky MountNC27801 35.9225-77.78



Excellent Service
Nick - Rocky Mount, NC 27804
Punctual & Informative.
Rocky MountNC27804 35.96-77.8325



Excellent Service!
Shirley - Rocky Mount, NC 27804
Great Service
Rocky MountNC27804 36.015-77.88
Response from Jackson & Sons:
We're so glad you enjoyed your experience with us. Thank you for the positive review!




Excellent Service!
Michael - Rocky Mount, NC 27803
Rocky MountNC27803 35.945-77.855




Excellent job !!
Bernice - Rocky Mount, NC 27801
Job well done !!
Rocky MountNC27801 35.955-77.755



We are satofied we went with this company
LaTanya - Rocky Mount, NC 27801
Thank you Derek.
Rocky MountNC27801 35.9325-77.78



Excellent Service
Landan - Rocky Mount, NC 27804
Derek was great and very knowledgeable.
Rocky MountNC27804 35.99-77.8125



Excellent and easy!
Tina - Rocky Mount, NC 27804
Chris was great, respectful and knowledgeable. He was even sweet with our dogs who wouldn’t stop barking. Excellent job - thank you!
Rocky MountNC27804 35.9925-77.8825



Excellent Service
Victor - Rocky Mount, NC 27804
Rocky MountNC27804 35.975-77.875




Excellent work
Ahmad - Rocky Mount, NC 27804
Rocky MountNC27804 35.9575-77.845




Excellent service!
Shaun - Rocky Mount, NC 27804
Rocky MountNC27804 35.9925-77.8775




Excellent Service!
Spiro - Rocky Mount, NC 27804
Aidan was thorough, skilled, patient and generous with his knowledge in troubleshooting and communicating the probable issue and applying a potential solution. Also he was genuinely enjoyable to interact and communicate with.
Rocky MountNC27804 35.97-77.8925



Excellent Work!
Michael - Rocky Mount, NC 27803
Audonel was exceptional! He and the guy working with him were nice, professional, and they really made short work out of the install.
Rocky MountNC27803 35.945-77.855



He is great to work with.
Michael - Rocky Mount, NC 27803
Bryce was very knowledgeable, and took the time to answer all my questions.
Rocky MountNC27803 35.945-77.855



Excellent!
Michael - Rocky Mount, NC 27803
Noah was very friendly, and very knowledgeable!
Rocky MountNC27803 35.945-77.855



Awesome Service Experience
ROCKY - Rocky Mount, NC 27804
Rocky MountNC27804 35.955-77.825




Awesome guy
LITTLE - Rocky Mount, NC 27803
Your company is very lucky to have Kenneth Chandler as an employee. I was very impressed with his ability to troubleshoot to find and fix the problem faster than I expected and on a holiday!!! Super polite and all around great guy!! Hope we have no more problems but if we do my wife and I hope we get him again!!
Rocky MountNC27803 35.9125-77.8125



Excellent service
Ricky - Rocky Mount, NC 27801
Technician was very courteous and professional.
Rocky MountNC27801 35.95-77.745



Great service
Spiro - Rocky Mount, NC 27804
Josh patiently answered my naive questions, diagnosed the problem and applied a temporary fix.
Rocky MountNC27804 35.97-77.8925



Excellent job !!
Bernice - Rocky Mount, NC 27801
Good service as always !! Professional technician !!
Rocky MountNC27801 35.955-77.755



Excellent Service
Victor - Rocky Mount, NC 27804
Kenny was great. Repair our computer, cleaned the coils and got us on a service plan. He was very friendly and informed us of our options!!
Rocky MountNC27804 35.975-77.875



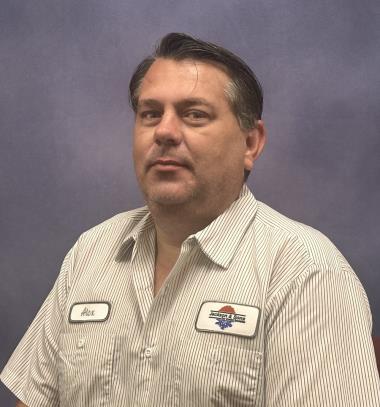
Alex R.
Found a mainline stoppage in the house. Pulled the toilet and ran sewer machine through the mainline and cleared paper towels from the main sewer line and then reset the toilet.
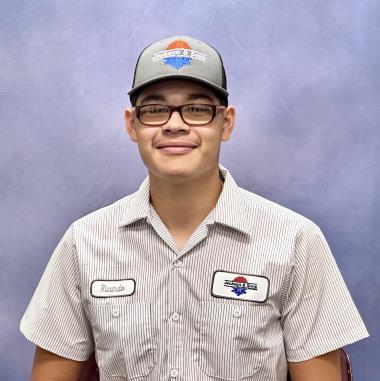
Ricardo T.
Tech washed and serviced unit and found no challenges at this time.
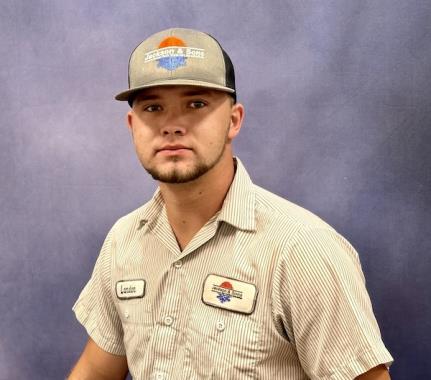
Landen H.
Tech washed and serviced both units and found no challenges at this time. (Both units are 6 months old) both units are up heating properly after today’s visit.
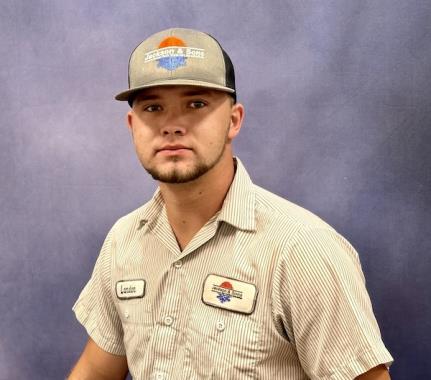
Landen H.
Tech washed and serviced unit and found evap coils to be rusted and corroded but no leaks at this time customer is aware of findings and units age. Unit is up cooling properly after todays visit.
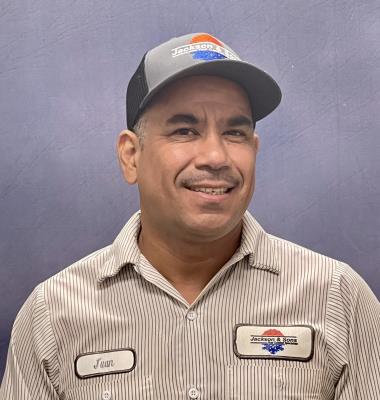
Juan R.
Install (2) 5 Ton OxBox Condensing Units
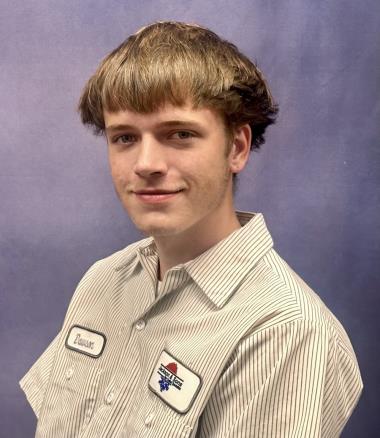
Dawson M.
Tech serviced and cleaned unit. Customer uses own filters. Upon arrival tech found condensate drain line cracked and laying on ground. Tech faced no challenges this visit. Tech recommends replacing uv bulb because it’s getting near its life span of 3 years. Tech also recommends plasma air to reduce bacteria build up and improve air quality. Unit is heating and cooling efficiently. Customer declined all recommendations at this time.
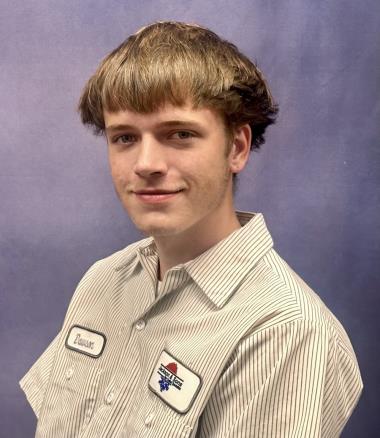
Dawson M.
Tech serviced and cleaned unit. Tech found blower capacitor reading at 5.5/7.5. Tech also found fan side of condenser capacitor reading at 4.30/5. Tech recommends replacing both capacitors. Customer will call in when ready to move forward with repairs. Tech faced no other challenges at this time. Unit is heating and cooling efficiently.
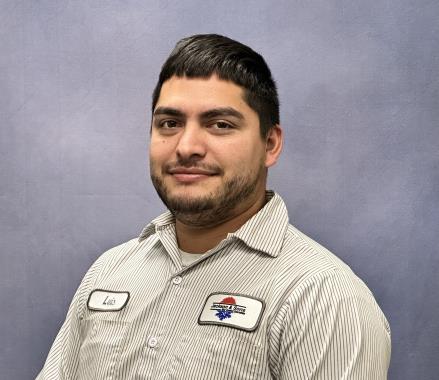
Luis R.
Technicians returned to replace heat exchanger and blower wheel and shaft with bearings. Technician reran gas piping and started system up heat exchanger started up and ran when blower tuned on control board blew and fuses blew as well technician suspected wiring for motor was not correct and shorted out the control board. Office will quote out board.
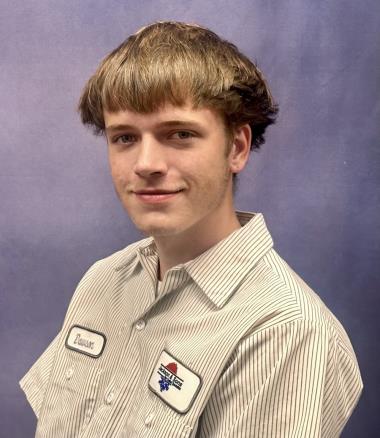
Dawson M.
Tech serviced unit. Upon arrival tech found water spicket in the front working but one in the back by the unit was not. Tech informed customer. Tech found excessive bacteria build up inside furnace. Tech found evaporator coil to be severely rusted. Tech believes a small leak is starting to form(tech took a video). Tech also found condenser coils to have excessive build up and recommends getting it cleaned out. Unit is heating and cooling efficiently. Customer wants an estimate on new evaporator coil.
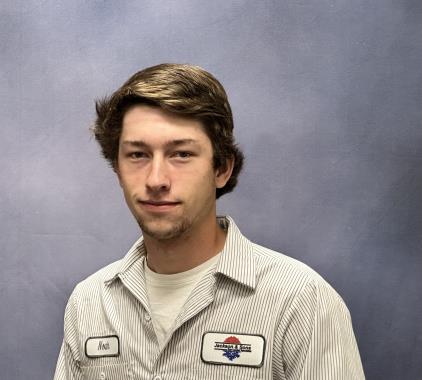
Noah C.
Returned to replace inducer draft assembly, installed new inducer and tested. System is back up and heating. Recommended investing in maintenance agreement.
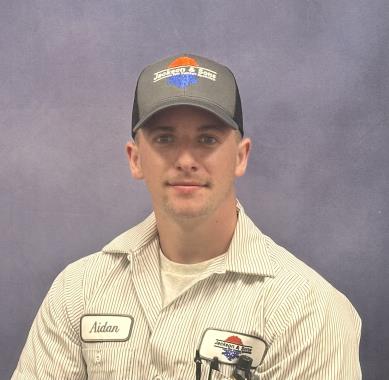
Aidan T.
— Tech replaced faulty defrost thermostat on RTU #3 (front) and confirmed proper defrost operation. Confirmed refrigerant pressures on RTU #2 are within specifications according to PT chart. — Both systems are operating normally at this time with both thermostats satisfied at 65 degrees at tech departure. Emailed bill.
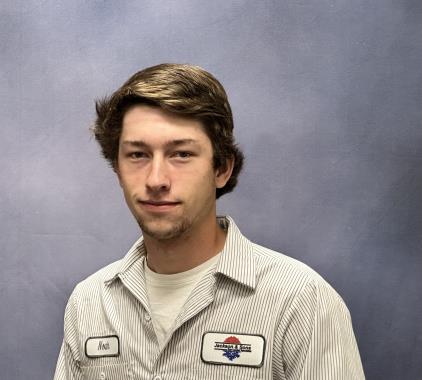
Noah C.
Upon arrival tech found failed inducer draft motor. Motor is seized up and will not turn freely. Gave estimate for warranty inducer replacement. Customer approved, need to get inducer motor and return to repair.

Chris A.
Tech washed and serviced unit, tech found rusty evaporator coil but no leaks detected. Unit is heating with a delta T of 17. Tech recommend media filters for both returns due to filters being dirty. Customer not interested.
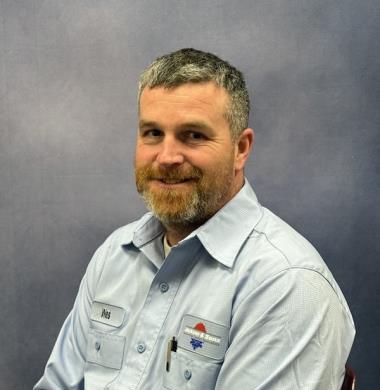
Wes B.
— Performed CMA Full Service on 3 Packaging Heat Pump Systems. All 3 Systems tested good and back to working condition.
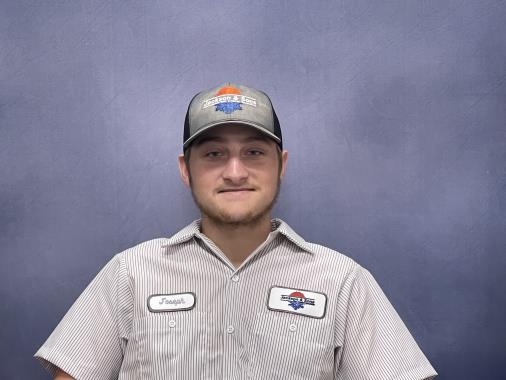
Joseph C.
Tech found multiple leaks in water coil spraying water out, tech cut water off in the mean time, will need field supervisor to come verify tomorrow due to age and cost of repairs.
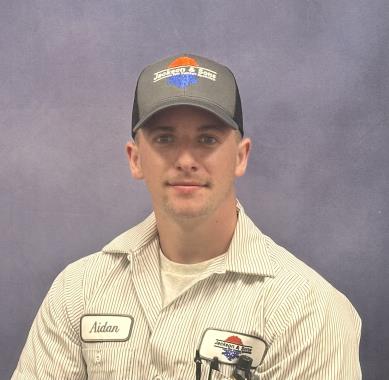
Aidan T.
- Upon arrival tech was informed that the two Trane RTUs that service the dining area and prepping counter at the front of the building were not operating properly. Both thermostats read 59 degrees upon arrival. (RTU #2 - Center) - Found loose blower belt and increased tension to ensure proper airflow. Observed low refrigerant pressures (45.1/282.6) and performed leak search level 3, finding no leaks. - Advised customer that a proper leak search could not be performed on outdoor coil due to weather conditions and recommended leak freeze solution and recharge, approximately 3lbs. Customer approved leak freeze and recharge. Tech installed leak freeze and charged 2lbs 1oz R-410A according to PT chart and confirmed heat strip and defrost operation with forced defrost and sensor-induced defrost. (RTU #3 - Front) - Found loose blower belt and increased tension to ensure proper airflow. Confirmed accurate refrigerant charge (77.3/325.0 39 degree OD ambient, 59 degree ID DB) per PT chart (
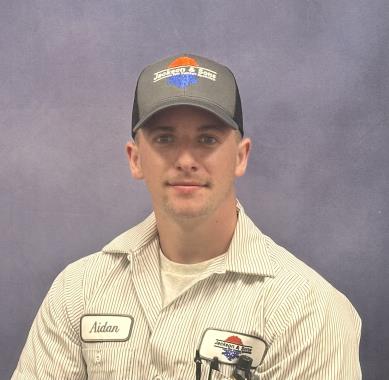
Aidan T.
- Upon arrival, tech found thermostat satisfied at 73 degrees. - Adjusted temperature and observed normal operation for 15 minutes. Confirmed heat strip and defrost operation. - Advised customer that the blower will run on a timer after the thermostat is satisfied and cold air will be distributed for short period of time while the heat pump starts up. System is operating normally at this time with delta T reading 41 degrees with heat strips.
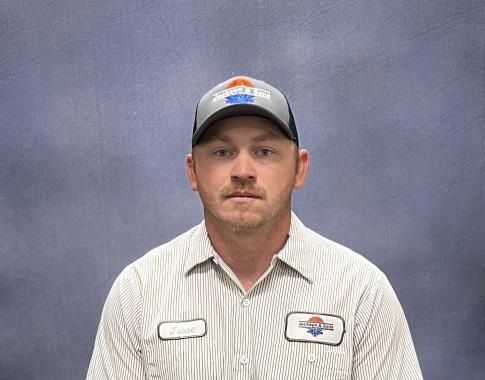
Jesse J.
Trane Furnace S8X1B080M4PSC Trane, S8X1, 80,000 BTU, Furnace Quantity: 1 Other Air Quality CUSTOM-29BJHR Plasma Air 602 Quantity: 1 Other Thermostats CUSTOM-JRKFUQ Honeywell - Wi-Fi VisionPRO 8000 (Package Systems) Quantity: 1 ICM Surge Protector Quantity: 1 Replace Non-Fused Electrical Disconnect Quantity: 1

Amber W.
Install 2 Ton Trane Packaged Unit With WiFi Programmable Thermostat
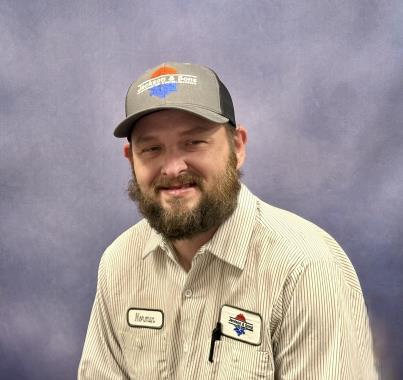
Norman A.
Flapper and fill valve in brake room restroom Brake room sink faucet is leaking when turn on need replace Front office toilet need be replaced tank is cracked and angle stop on same bathroom on hot side need replaced Bad fill valve in back bathroom Bad fill valve in warehouse bathroom Try run the snake threw drain it is claps all it doing is gridding my snake head down drain need to be replaced advise them we couldn’t do that
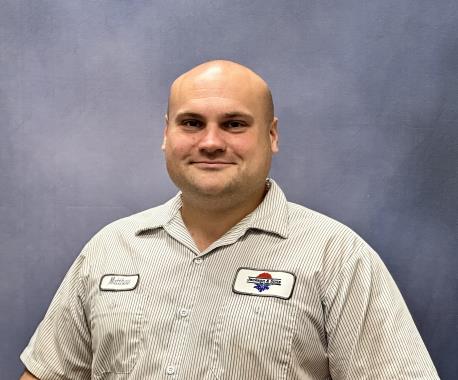
Matthew L.
Tech found older ICP gas pack not heating due to unit receiving only 120 volts of the 240 volt line voltage. 25 amp breaker was not sending 1 of the 2 legs of power. Tech bumped breaker and it remade connection. Breaker appears older. Tech recommended replacing breaker to ensure unit continues to get line voltage. Data tag calls for minimum circuit protection of 25 amps and max circuit protection of 40 amps. 40 amp breaker is appropriate. Tech observed burners light normally. Inspected heat exchanger and found no cracks or holes. Customer approved replacing breaker. No housecall per PSA. Maintenance scheduled Monday the 17 between 8 and 10.
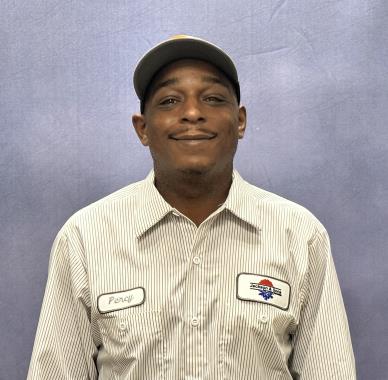
Percy M.
PERFORMED CMA FULL SERVICE ON 4 SPLIT SYSTEMS, 2 PACKAGE HEAT PUMP SYSTEMS AND 1 MINI SPLIT SYSTEM. PACKAGE HEAT PUMP #2 FAN CAPACITOR RATED FOR 10mf TESTED WEAK AT 8.67mf. CAPACITOR DUE FOR FAILURE, RECOMMEND REPLACEMENT OF CAPACITOR. THERE IS AN ESTIMATE ATTACHED TO THIS INVOICE FOR REPLACEMENT OF CAPACITOR.

Caleb S.
Provided estimate to replace duct system
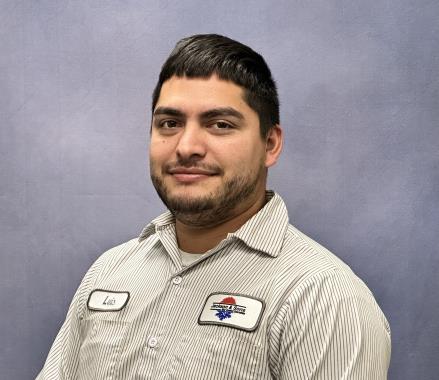
Luis R.
50 amp breaker technician replaced the breaker system is heating properly at this time.

Audonel G.
Trane Condenser (XR14) 4TWR4024N1000A Trane, XR14 Heat Pump, 2 Ton, Heat Pump Quantity: 1 Trane Fan Coil TEM4B0B24M21SA Trane, M Series TEM4, 2 Ton, Air Handler Quantity: 1 Other Services CUSTOM-0M1HWW ESA Quantity: 1 Other HVAC Add-Ons CUSTOM-E5QS3T EZ Trap Quantity: 1 Other HVAC Add-Ons CUSTOM-MF3IRD Filter Dryer Quantity: 1 Other HVAC Add-Ons CUSTOM-YGY31S BAYHTR1505 (Split System) Quantity: 1 Other Thermostats CUSTOM-9HQCG8 Honeywell - Wi-Fi VisionPRO® 8000 ( Trane Split Systems) Quantity: 1 14" Start Collar Quantity: 1 32x60 Drain Pan Quantity: 1 36X40 Pad Quantity: 1 EZ Trap Quantity: 1 Float Switch Quantity: 1 Foam Blocks (6) Quantity: 1 ICM Surge Protector Quantity: 1 Level Pad Quantity: 1